Top Carbide Roller Manufacturers Comprehensive Guide Sourcing from China.
Top carbide roller in China introduce,list main products and website if have
One of the top carbide roller manufacturers in China is Zhuzhou Lizhou Cemented Carbide Co., Ltd. They specialize in producing high-quality carbide rollers for various industrial applications. Some of their main products include tungsten carbide rollers, carbide wire drawing dies, carbide roller rings, and carbide roller guides.
Zhuzhou Lizhou Cemented Carbide Co., Ltd. is known for their advanced technology, strict quality control, and excellent customer service. Their carbide rollers are widely used in industries such as wire drawing, steel rolling, and metal forming.
For more information about Zhuzhou Lizhou Cemented Carbide Co., Ltd. and their products, you can visit their official website at www.zzlizhou.com. You can browse through their product catalog, learn about their manufacturing process, and contact their sales team for inquiries or orders.
With their high-quality products and dedicated customer service, Zhuzhou Lizhou Cemented Carbide Co., Ltd. has earned a reputation as one of the leading carbide roller manufacturers in China. Their commitment to innovation and excellence makes them a trusted partner for businesses in need of reliable carbide roller solutions.
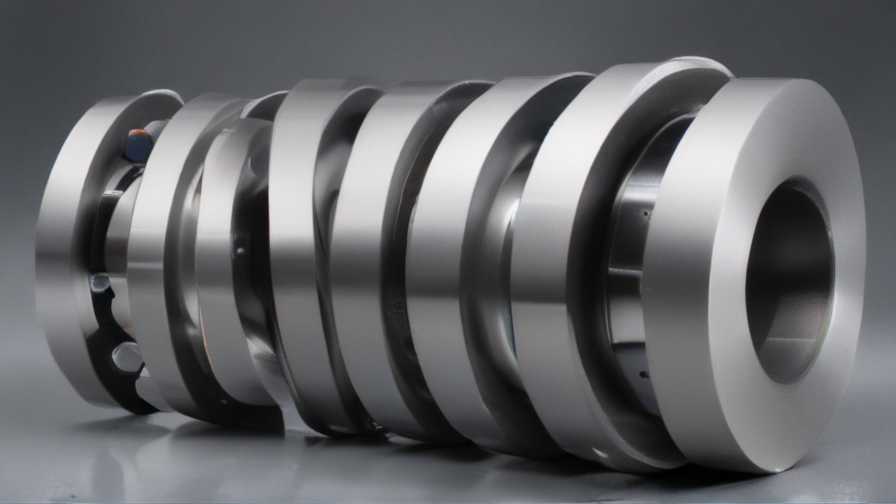
Types of carbide roller
Carbide rollers are commonly used in various industrial applications due to their superior resistance to wear and corrosion. There are several types of carbide rollers available, each designed for specific uses and applications.
1. Tungsten carbide rollers: Tungsten carbide is one of the most commonly used materials for carbide rollers due to its high hardness and wear resistance. Tungsten carbide rollers are ideal for applications where high wear resistance and durability are required, such as wire drawing and rolling mills.
2. Silicon carbide rollers: Silicon carbide rollers are another popular choice for industrial applications due to their excellent heat resistance and thermal conductivity. Silicon carbide rollers are commonly used in high-temperature applications, such as in the manufacturing of ceramic products or in metal casting.
3. Boron carbide rollers: Boron carbide rollers are known for their exceptional hardness, making them suitable for applications that require high wear resistance and precision, such as in the production of precision bearings or cutting tools.
4. Titanium carbide rollers: Titanium carbide rollers are often used in applications that require high strength and wear resistance. Titanium carbide rollers are commonly used in the manufacturing of steel and aluminum products, as well as in wire drawing and sheet metal forming applications.
Overall, carbide rollers offer superior performance and longevity compared to traditional steel or rubber rollers, making them an essential component in various industrial processes. By choosing the right type of carbide roller for a specific application, manufacturers can improve efficiency, reduce maintenance costs, and increase productivity.
Pros and Cons of Using carbide roller
Carbide rollers are widely used in various industrial applications due to their high hardness, wear resistance, and thermal conductivity. Here are some pros and cons of using carbide rollers:
Pros:
1. Wear Resistance: Carbide rollers are extremely wear-resistant, making them ideal for applications where the roller is subjected to high levels of friction and wear.
2. High Hardness: Carbide rollers have a high hardness level, which ensures a longer service life and reduces the need for frequent replacements.
3. Thermal Conductivity: Carbide rollers have excellent thermal conductivity, allowing for efficient heat dissipation and preventing overheating during operation.
4. Precision Machining: Carbide rollers can be machined to very precise tolerances, making them suitable for applications that require high precision and accuracy.
5. Corrosion Resistance: Carbide rollers are resistant to corrosion, making them ideal for use in harsh environments or exposure to corrosive materials.
Cons:
1. Cost: Carbide rollers are more expensive than traditional roller materials, which can be a significant drawback for budget-conscious applications.
2. Brittleness: Carbide is brittle and may chip or crack under certain conditions, leading to potential damage to the roller.
3. Difficult to Repair: In case of damage, carbide rollers are difficult to repair compared to other roller materials, and replacement may be necessary.
4. Weight: Carbide rollers are heavier than some other roller materials, which can affect the overall weight and balance of the machinery.
5. Limited Availability: Carbide rollers may not be as readily available as other roller materials, which could lead to longer lead times for replacement or repairs.
In conclusion, carbide rollers offer excellent wear resistance, hardness, and thermal conductivity, making them ideal for various industrial applications. However, the higher cost, brittleness, and limited availability are some potential drawbacks to consider when choosing carbide rollers for a specific application.
carbide roller Reference Specifications (varies for different product)
Carbide rollers are an essential component in various industrial applications, providing wear resistance and longer service life compared to traditional steel rolls. These rollers are commonly used in high-speed wire and rod mills, as well as in the paper, textile, and printing industries.
There are several key specifications to consider when selecting carbide rollers, including dimensions, tolerances, surface finish, hardness, and coating options. The dimensions of the roller, such as diameter, length, and grooving pattern, must be carefully chosen to match the specific requirements of the application. Tolerances are critical to ensure proper fit and alignment within the machinery.
Surface finish is another important factor, as it can impact the performance and lifespan of the roller. A smooth surface finish is typically desired to minimize friction and wear. Carbide rollers are known for their hardness, which provides excellent wear resistance and durability in harsh operating conditions. The hardness can be customized based on the specific application requirements.
In some cases, carbide rollers may be coated with a protective layer to further enhance their performance characteristics. Common coating options include chrome plating, tungsten carbide coating, and various ceramic coatings. These coatings can improve corrosion resistance, reduce friction, and enhance wear properties.
Overall, selecting the right carbide roller specifications is crucial to ensure optimal performance and longevity in industrial applications. By considering factors such as dimensions, tolerances, surface finish, hardness, and coating options, manufacturers can choose the best roller for their specific needs.
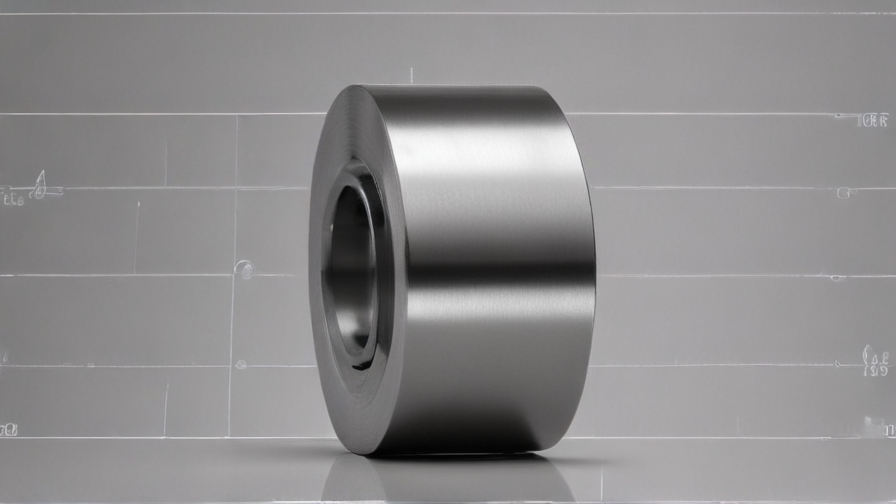
Applications of carbide roller
Carbide rollers are widely used in various industrial applications due to their high durability, wear resistance, and ability to withstand high temperatures. Some common applications of carbide rollers include:
1. Metal forming: Carbide rollers are commonly used in the metal forming industry for processes such as rolling, drawing, and extrusion. The high hardness and wear resistance of carbide rollers ensure a long service life and consistent performance, even under high pressures and temperatures.
2. Wire and cable production: Carbide rollers are used in the production of wires and cables to ensure precise sizing and shaping of the final products. The high hardness of carbide rollers helps to maintain tight tolerances and reduce wear on the rollers during the production process.
3. Printing and packaging: Carbide rollers are used in printing and packaging industries for applications such as rolling, embossing, and laminating. The high wear resistance of carbide rollers ensures high-quality printing and packaging results with minimal downtime for roller replacement.
4. Textile manufacturing: Carbide rollers are used in the textile industry for processes such as sizing, calendering, and embossing. The high hardness and smooth surface finish of carbide rollers help to achieve uniform fabric properties and textures.
5. Food processing: Carbide rollers are used in food processing industries for applications such as dough rolling, pasta extrusion, and cookie forming. The hygienic properties of carbide rollers make them ideal for food contact applications, and their high wear resistance ensures consistent product quality.
Overall, carbide rollers are versatile components that find applications in various industries where high wear resistance, durability, and precision are required. Their superior performance and long service life make them a preferred choice for many industrial applications.
Material of carbide roller
Carbide rollers are typically made from tungsten carbide, a type of ceramic material that is known for its hardness and resistance to wear. Tungsten carbide is a compound of tungsten and carbon, with a chemical formula WC. It is one of the hardest materials available, second only to diamond.
Tungsten carbide rollers are commonly used in industrial applications where high wear resistance is required, such as in the manufacturing of metal wires, tubes, and sheet metal. The hardness of tungsten carbide allows these rollers to withstand the high pressures and temperatures involved in these processes without deforming or wearing down quickly.
In addition to tungsten carbide, carbide rollers may also be made from other types of carbide materials, such as titanium carbide and tantalum carbide. These materials offer similar characteristics to tungsten carbide, such as hardness and wear resistance, but may be used in specific applications where their unique properties are advantageous.
Overall, the choice of material for carbide rollers depends on the specific requirements of the application, such as the level of wear resistance needed, the operating conditions, and the desired lifespan of the rollers. Tungsten carbide remains the most popular choice due to its superior hardness and durability, making it a versatile material for a wide range of industrial applications.
Quality Testing Methods for carbide roller and how to control the quality
Quality testing methods for carbide rollers can include visual inspection, dimensional measurements, hardness testing, and metallurgical testing. Visual inspection involves examining the roller for any defects such as cracks, chips, or uneven wear. Dimensional measurements ensure that the roller meets the specified tolerances for diameter, length, and other critical dimensions. Hardness testing is important as carbide rollers need to have a certain level of hardness to ensure they can withstand wear and tear. Metallurgical testing involves analyzing the composition of the carbide material to ensure it meets the required specifications.
To control the quality of carbide rollers, it is important to have a strict quality control process in place. This can include regular inspections during production, random sampling for testing, and strict adherence to quality standards. It is also important to work with reputable suppliers who provide high-quality carbide material and have a track record of producing reliable products. Additionally, having a robust quality management system in place can help identify and address any quality issues before they impact production or customer satisfaction. Regular audits and continuous improvement efforts can also help maintain and improve the quality of carbide rollers.
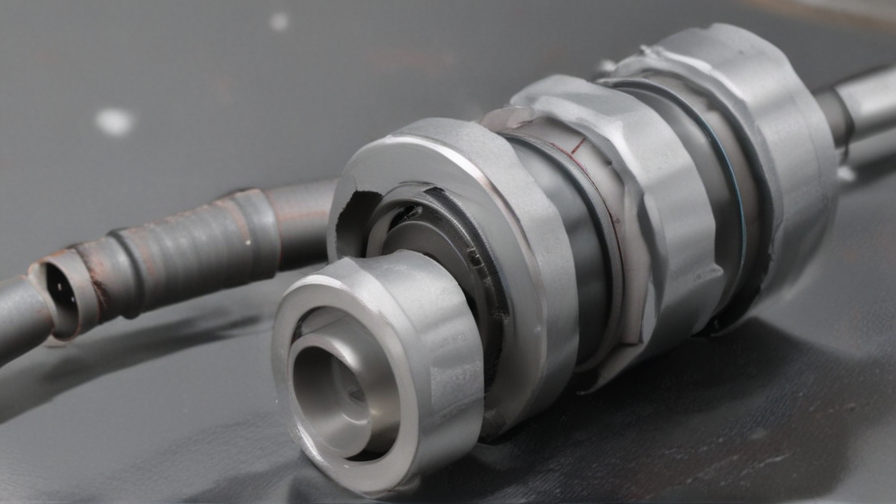
The Work Process and how to use carbide roller
Carbide rollers are commonly used in various industries for tasks such as forming, embossing, or calibrating materials. The work process typically involves mounting the carbide roller onto a machine or equipment designed for the specific task at hand.
To use a carbide roller, start by securely attaching it to the designated machine using the appropriate mounting method. Make sure the roller is properly aligned and adjusted according to the requirements of the job.
Next, feed the material to be processed through the machine, ensuring it passes through the carbide roller smoothly. Adjust the pressure and speed of the roller as needed to achieve the desired result.
During operation, regularly inspect the carbide roller for any signs of wear or damage. If any issues are detected, stop the machine immediately and address them before continuing.
It is important to note that carbide rollers are designed for specific tasks and materials, so it is crucial to use them within their recommended capabilities. Avoid exceeding the maximum operational limits to prevent premature wear and possible damage to the roller.
After completing the job, properly clean and maintain the carbide roller to ensure its longevity and optimal performance for future tasks. Store it in a safe and dry place to prevent any potential damage or deterioration.
By following these guidelines and using a carbide roller within its recommended parameters, you can effectively process materials and achieve high-quality results in various industries.
carbide roller Importing questions including Cost,Supplier,Sample,Certification and Market
Importing carbide rollers can be a profitable business opportunity, but there are some important considerations to keep in mind before making a purchase.
Cost: The cost of importing carbide rollers can vary depending on factors such as quantity, quality, and supplier. It is important to compare prices from different suppliers to ensure you are getting the best deal possible.
Supplier: When choosing a supplier for carbide rollers, it is important to consider factors such as reputation, quality of products, and reliability. Look for suppliers who have a good track record of delivering high-quality products on time.
Sample: Before making a bulk purchase of carbide rollers, it is a good idea to order a sample to test the quality and durability of the product. This can help you make an informed decision before committing to a larger order.
Certification: Make sure that the carbide rollers you are importing meet any relevant certification requirements in your country. This can help ensure that the products are safe and of high quality.
Market: Consider the demand for carbide rollers in your target market before importing them. Conduct market research to understand the needs and preferences of potential customers, and tailor your product offerings accordingly.
Overall, importing carbide rollers can be a lucrative business opportunity if done correctly. By carefully considering factors such as cost, supplier, sample testing, certification, and market demand, you can increase your chances of success in this venture.
How to find and select check reliable carbide roller manufacturers in China
When searching for reliable carbide roller manufacturers in China, there are a few key steps to follow to ensure you are selecting a trustworthy and high-quality supplier.
Firstly, start by researching and compiling a list of potential manufacturers through online platforms such as Alibaba, Made-in-China, or Global Sources. Look for companies with a good reputation, positive reviews, and a history of exporting carbide rollers to international markets.
Next, reach out to these manufacturers and request more information about their products, production process, and quality control measures. Ask for samples or visit their factories if possible to inspect their facilities and verify their capabilities.
In addition, make sure to inquire about their experience in manufacturing carbide rollers and their ability to customize products according to your specific requirements. A reliable manufacturer should be able to provide references and certifications to demonstrate their quality standards and compliance with industry regulations.
When selecting a manufacturer, consider factors such as price competitiveness, lead times, payment terms, and after-sales support. It is also important to establish clear communication channels and ensure a solid contractual agreement to protect your interests.
Overall, by conducting thorough research, verifying credentials, and communicating effectively with potential manufacturers, you can find a reliable carbide roller manufacturer in China to meet your business needs.
Background Research for carbide roller manufacturers Companies in China, use qcc.com archive.org importyeti.com
When searching for carbide roller manufacturers in China, it is important to utilize resources such as qcc.com, archive.org, and importyeti.com to find reputable companies. These websites can provide valuable information on the background and track record of manufacturers before making a decision on which company to do business with.
Qcc.com is a reliable platform that offers detailed company profiles, including information on their product range, production capacity, and certifications. This can help in determining the suitability of a manufacturer for specific requirements.
Archive.org can be used to access historical data on the company, including their website and any previous customer reviews or feedback. This can give insight into the company’s reputation and customer satisfaction levels.
Importyeti.com is a useful tool for finding global suppliers and manufacturers, including those in China. It provides data on shipments, manufacturing capabilities, and customer reviews, making it easier to identify potential partners for carbide roller production.
By utilizing these resources, businesses can make more informed decisions when selecting a carbide roller manufacturer in China. It is essential to research thoroughly and consider factors such as quality, reliability, and reputation before entering into any partnership.
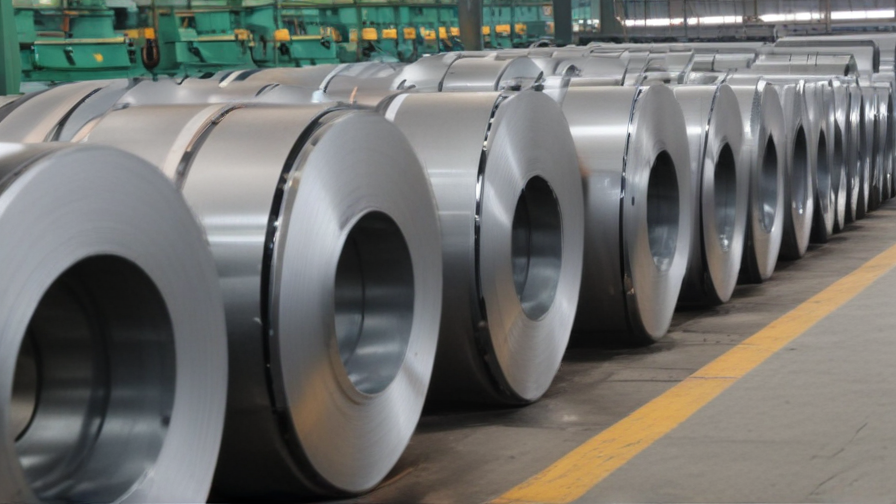
Price Cost Research for carbide roller manufacturers Companies in China, use temu.com and 1688.com
When conducting price cost research for carbide roller manufacturers in China, platforms such as Temu.com and 1688.com can be valuable resources. These websites offer a wide range of options for identifying and comparing the prices of carbide rollers from different manufacturers in China.
Using these platforms, one can search for specific types of carbide rollers and compare the prices offered by various manufacturers. It is also possible to filter the search results based on factors such as the material used, size, and other specifications.
In addition, one can reach out directly to the manufacturers through these platforms to inquire about bulk pricing, customization options, and other details that may impact the overall cost of the carbide rollers.
Overall, by utilizing Temu.com and 1688.com for price cost research, one can gain valuable insights into the offerings of carbide roller manufacturers in China and make informed decisions when sourcing these products for their business.
Shipping Cost for carbide roller import from China
The cost of shipping carbide rollers from China will depend on several factors such as the weight and dimensions of the shipment, the mode of transport chosen, and the distance it needs to travel. Generally, the most common modes of shipping from China to other countries are air freight, sea freight, or courier services.
For small and lightweight shipments, using a courier service like DHL, UPS, or FedEx may be the fastest and most convenient option, but also the most expensive. Shipping costs can range from $50 to $200 or more, depending on the size and weight of the package.
For larger shipments, sea freight is often the most cost-effective option, especially for heavy or bulky items like carbide rollers. Shipping cost for sea freight can vary greatly depending on the volume of the shipment, the shipping route, and any additional services required. On average, shipping costs for a standard 20ft container from China to other countries range from $800 to $2000.
Alternatively, air freight is a faster but more expensive option for shipping carbide rollers. The cost of air freight can vary depending on the weight, size, and destination of the shipment. On average, shipping costs for air freight from China to other countries range from $3 to $8 per kilogram.
It is important to consider all these factors when calculating the shipping costs for importing carbide rollers from China to ensure that the cost does not exceed your budget. Additionally, working with a reputable freight forwarder or shipping company can help you navigate the complexities of international shipping and find the most cost-effective solution for your specific needs.
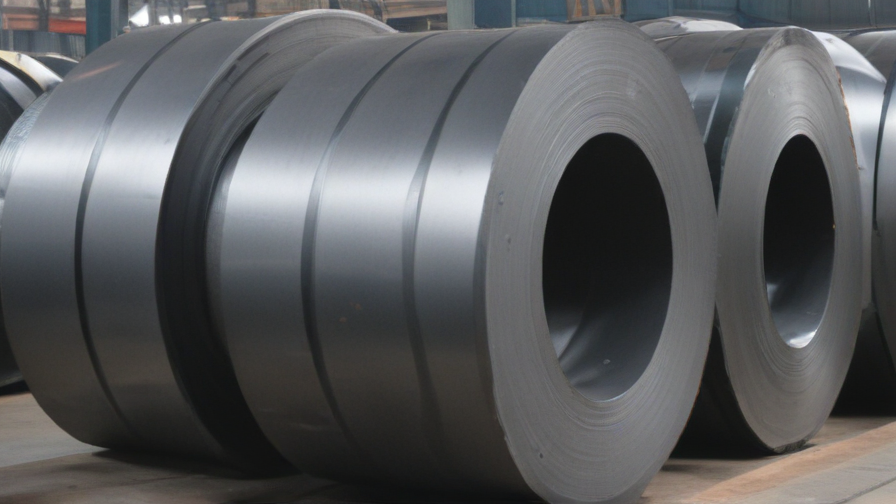
Compare China and Other carbide roller Markets: Products Quality and Price,Visible and Hidden Costs
China is a major producer of carbide rollers, providing a wide range of products in terms of quality and price. The quality of carbide rollers produced in China can vary significantly depending on the manufacturer. While some Chinese manufacturers offer high-quality carbide rollers that meet international standards, others may produce lower-quality products that are not as durable or reliable.
In terms of price, Chinese carbide rollers are generally more competitive compared to other markets such as Europe or the United States. This is due to lower production costs in China, including lower labor costs and manufacturing expenses. As a result, Chinese carbide rollers are often more affordable for consumers, making them a popular choice in the global market.
However, there are also visible and hidden costs associated with purchasing carbide rollers from China. Visible costs include shipping and import duties, which can add to the overall price of the product. Hidden costs, on the other hand, may include issues related to product quality and reliability, as well as the potential for delays in delivery or communication barriers with Chinese manufacturers.
Overall, while China offers a wide range of carbide rollers at competitive prices, buyers should be cautious of potential quality issues and hidden costs when sourcing products from this market. It is essential to conduct due diligence and work with reputable manufacturers to ensure the quality and reliability of carbide rollers purchased from China.
Custom Private Labeling and Branding Opportunities with Chinese carbide roller Manufacturers
If you are looking for custom private labeling and branding opportunities with Chinese carbide roller manufacturers, you are in the right place. Our manufacturers specialize in producing high-quality carbide rollers that are ideal for a wide range of industrial applications.
With our custom private labeling and branding services, you can have your company logo, colors, and other branding elements printed or engraved on the carbide rollers. This allows you to create a unique and professional look for your products, helping to enhance your brand identity and visibility in the market.
Our manufacturers have the expertise and experience to work closely with you to develop custom designs that meet your specifications and requirements. Whether you are looking for a specific size, shape, or coating for your carbide rollers, we can help you create the perfect solution for your needs.
By partnering with our manufacturers for custom private labeling and branding, you can differentiate your products from the competition and attract more customers to your brand. With our high-quality carbide rollers and personalized branding options, you can enhance the overall value of your products and increase customer loyalty and satisfaction.
Contact us today to learn more about our custom private labeling and branding opportunities with Chinese carbide roller manufacturers. We look forward to helping you elevate your brand presence and grow your business with our customizable solutions.
Tips for Procurement and Considerations when Purchasing carbide roller
When procuring carbide rollers, it is important to consider the following tips to ensure that you acquire a product that meets your needs and expectations:
1. Quality: Choose a reputable supplier that offers high-quality carbide rollers. Look for manufacturers with a proven track record of producing durable and reliable products.
2. Material: Carbide rollers are typically made from tungsten carbide, which is known for its hardness and wear resistance. Ensure that the carbide roller you choose is made from high-quality tungsten carbide material.
3. Size and specifications: Consider the size and specifications of the carbide roller that you need for your specific application. Make sure that the roller dimensions and tolerances meet your requirements.
4. Coating: Some carbide rollers come with a coating to enhance their performance and durability. Consider whether you need a coated carbide roller for your application.
5. Price: While cost is an important factor, prioritize quality over price when selecting a carbide roller. Cheaper options may end up costing you more in the long run if they require frequent replacement or repairs.
6. Maintenance: Consider the maintenance requirements of the carbide roller and choose a product that is easy to clean and maintain.
7. Warranty: Check if the carbide roller comes with a warranty to ensure that you are protected in case of any defects or issues with the product.
By following these tips and considerations, you can ensure that you purchase a high-quality carbide roller that is suitable for your specific application and provides long-lasting performance.
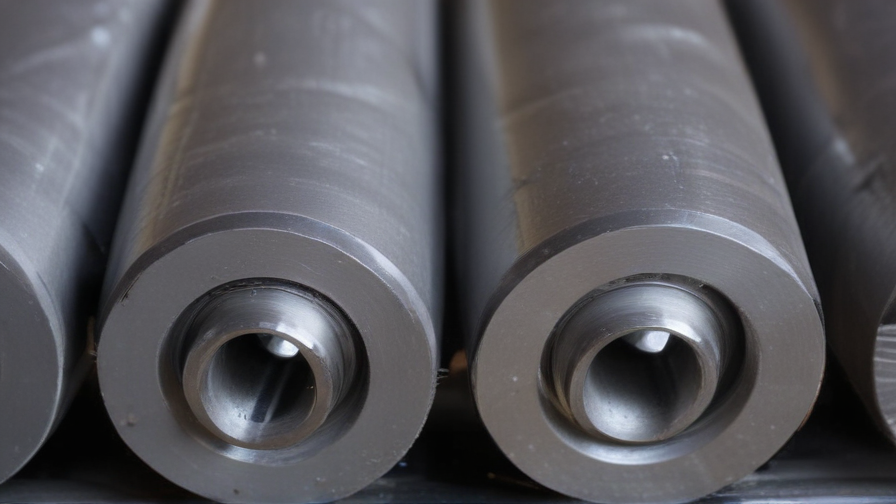
FAQs on Sourcing and Manufacturing carbide roller in China
1. How can I source carbide rollers from China?
You can source carbide rollers from China through various avenues such as online marketplaces, trade shows, and industrial exhibitions, as well as working with sourcing agents or directly contacting manufacturers. It is important to conduct thorough research, verify the credibility of suppliers, and request samples before placing bulk orders.
2. What is the manufacturing process for carbide rollers in China?
The manufacturing process for carbide rollers in China typically involves the following steps: selecting high-quality raw materials, such as tungsten carbide, mixing and compressing the raw materials into the desired shape using specialized machinery, sintering the compacted material in a high-temperature furnace to bond the particles together, precision grinding and finishing the rollers to achieve the desired dimensions and surface quality, and quality testing to ensure the rollers meet the required specifications.
3. How can I ensure the quality of carbide rollers manufactured in China?
To ensure the quality of carbide rollers manufactured in China, it is important to work with reputable suppliers who have a track record of producing high-quality products. You can also request samples for testing, conduct factory audits, and implement quality control measures such as on-site inspections and third-party testing. Communicating clearly with manufacturers about your specific requirements and expectations is also crucial in ensuring the quality of the carbide rollers.
4. Are there any potential challenges or risks associated with sourcing and manufacturing carbide rollers in China?
Some potential challenges or risks associated with sourcing and manufacturing carbide rollers in China include language barriers, cultural differences, intellectual property protection, quality control issues, and supply chain disruptions. It is important to address these challenges proactively by conducting due diligence, negotiating clear agreements, and establishing a strong relationship with suppliers to mitigate risks and ensure a successful sourcing and manufacturing process.
Why contact sourcifychina.com get free quota from reliable carbide roller suppliers?
Sourcifychina.com is a trusted platform that connects businesses with reliable suppliers, including carbide roller suppliers. By contacting Sourcifychina.com, you can easily obtain a free quota from reputable carbide roller suppliers, allowing you to compare prices, quality, and services before making a decision.
Utilizing Sourcifychina.com to secure quotes from multiple suppliers can help you find the best deal and ensure that you are working with a supplier that meets your specific requirements. This can save you time and effort in the sourcing process, as Sourcifychina.com has already vetted and verified the suppliers listed on their platform.
In addition, working with reliable carbide roller suppliers can ensure that you receive high-quality products that meet your performance standards. These suppliers have the experience and expertise to deliver consistent and reliable products, helping you maintain the quality of your own products or services.
Overall, contacting Sourcifychina.com to get a free quota from reliable carbide roller suppliers is a smart business move that can help you streamline your sourcing process, find the best supplier for your needs, and ultimately improve the quality of your products.
Contact [email protected] Whatsapp 86 15951276160