Top Machining Precision Manufacturers Comprehensive Guide Sourcing from China.
Top machining precision in China introduce,list main products and website if have
China is known for its top machining precision in various industries including automotive, aerospace, and electronics. One of the leading companies in China offering high precision machining services is TopWio Precision.
TopWio Precision specializes in CNC machining, turning, milling, and grinding services to meet the demands of tight tolerances and complex geometries. Their main products include precision components for automotive parts, aerospace components, medical equipment, and electronic devices. The company is equipped with advanced CNC machines and inspection equipment to ensure the highest quality and precision in their products.
Another prominent company in China known for its top machining precision is Shenzhen Jiuzhao Precision Technology Co., Ltd. They offer a wide range of precision machining services for industries like automotive, electronics, and telecommunications. Some of their main products include precision gears, shafts, and housings for various applications.
Both TopWio Precision and Shenzhen Jiuzhao Precision Technology Co., Ltd have websites where more information about their services and products can be found. TopWio Precision’s website is www.topwioprecision.com, and Shenzhen Jiuzhao Precision Technology Co., Ltd’s website is www.precmachining.com.
Overall, China’s top machining precision companies offer high-quality services and products to meet the demanding requirements of various industries worldwide.
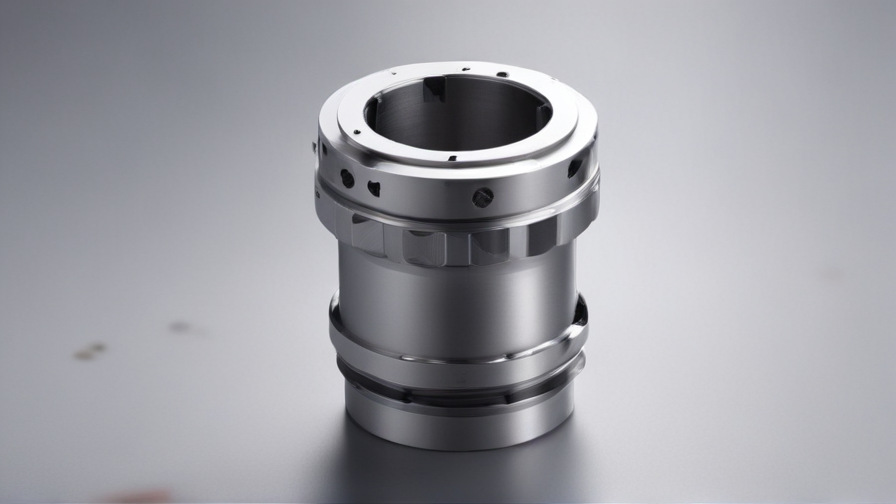
Types of machining precision
Machining precision refers to the level of accuracy and exactness that can be achieved during the production process. There are several types of machining precision that are used in various industries to create high-quality components and products.
1. Micro Machining Precision: This type of precision involves the fabrication of extremely small components with dimensions in the micrometer range. Micro machining requires specialized equipment and techniques to achieve the desired level of accuracy.
2. High Precision Machining: High precision machining involves the production of components with tight tolerances and high accuracy. This type of precision is commonly used in industries such as aerospace, automotive, and medical devices where the quality and performance of the products are crucial.
3. Ultra-Precision Machining: Ultra-precision machining is used to achieve sub-micron tolerances and surface finishes in the nanometer range. This type of precision is necessary for manufacturing components for advanced scientific instruments, semiconductor devices, and optical systems.
4. 5-Axis Machining Precision: 5-axis machining precision refers to the ability to machine complex geometries and contours on multiple axes simultaneously. This type of precision allows for more efficient and accurate production of parts with intricate shapes and features.
5. Swiss Machining Precision: Swiss machining precision is a specialized type of precision machining that is commonly used for producing small, high-precision components with tight tolerances. Swiss machining is ideal for applications where the production of small, complex parts is required.
Overall, the type of machining precision required will depend on the specific requirements of the component or product being produced. By choosing the appropriate type of precision machining, manufacturers can ensure the quality, accuracy, and performance of their products.
Pros and Cons of Using machining precision
Machining precision refers to the level of accuracy and consistency in the dimensions and surface finish of a part produced through machining processes. There are several pros and cons associated with using machining precision:
Pros:
1. Accuracy: Machining precision ensures that parts are manufactured to tight tolerances, resulting in highly accurate and reliable components.
2. Consistency: Machining precision allows for the production of identical parts with consistent dimensions and surface finish, ensuring quality and uniformity across batches.
3. Versatility: Machining precision can be applied to a wide range of materials, including metals, plastics, and composites, making it a versatile solution for various industries and applications.
4. Customization: Machining precision can be tailored to meet specific design requirements, allowing for the production of complex, customized parts.
5. Cost-effective: While initially more expensive than other manufacturing methods, machining precision can be cost-effective in the long run due to reduced scrap rates and the ability to produce high-quality parts with minimal post-processing.
Cons:
1. Time-consuming: Machining precision can be a time-consuming process, especially for complex parts or intricate designs, leading to longer lead times and potentially delaying production schedules.
2. Waste: Machining precision can generate a significant amount of waste, particularly in the form of chips and shavings, which may need to be disposed of or recycled.
3. Cost: As mentioned earlier, machining precision can be initially expensive due to the specialized equipment and skilled labor required, making it less cost-effective for small production runs or simple parts.
4. Limitations: Machining precision may have limitations in terms of the size and complexity of parts that can be produced, particularly for features with tight tolerances or intricate geometries.
5. Environmental impact: The energy-intensive nature of machining precision can result in a high carbon footprint, making it less environmentally friendly compared to other manufacturing methods.
In conclusion, machining precision offers benefits such as accuracy, consistency, versatility, customization, and cost-effectiveness, but drawbacks including time-consumption, waste generation, high cost, limitations, and environmental impact should be considered when deciding whether to use this manufacturing method.
machining precision Reference Specifications (varies for different product)
Precision machining refers to the process of creating components with very tight tolerances and high levels of accuracy. The reference specifications for machining precision can vary depending on the product being manufactured. Some common specifications include dimensional accuracy, surface finish, material properties, and geometric features.
Dimensional accuracy refers to the ability of a machined component to meet specified dimensions within a certain tolerance range. This is typically measured in microns or thousandths of an inch. Surface finish is another important specification, as it determines the smoothness and overall appearance of the machined part. Different surface finishes can be achieved through various machining techniques such as grinding, polishing, or lapping.
Material properties are crucial when machining precision components, as the choice of material can impact the machinability, durability, and performance of the final product. Material properties to consider may include hardness, toughness, thermal conductivity, and corrosion resistance.
Geometric features such as concentricity, parallelism, perpendicularity, and angularity also play a key role in precision machining. These features ensure that the components fit together correctly and function as intended.
In conclusion, precision machining requires strict adherence to reference specifications to produce high-quality components with the necessary tolerances and accuracy. By considering dimensional accuracy, surface finish, material properties, and geometric features, manufacturers can achieve the precision required for various applications.
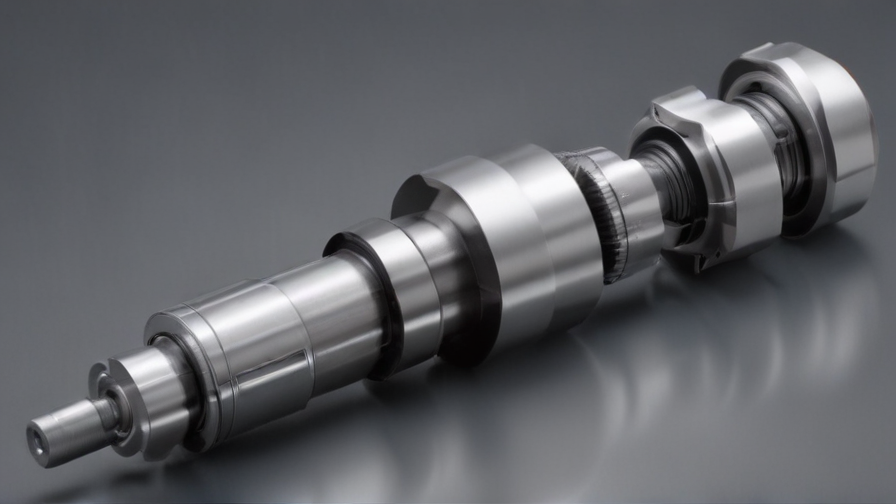
Applications of machining precision
Machining precision plays a crucial role in various industries and applications where tight tolerances and high accuracy are required. Some common applications of machining precision include:
1. Aerospace industry: Machining precision is essential in the manufacturing of aircraft components such as turbine blades, engine parts, and landing gear. The high accuracy and tolerances achieved through precision machining ensure the safety and reliability of aerospace vehicles.
2. Medical devices: Precision machining is used in the fabrication of medical devices such as implants, surgical instruments, and prosthetics. The precise dimensions and surface finishes achieved through machining ensure the compatibility and effectiveness of these devices in medical applications.
3. Automotive industry: Machining precision is vital in the production of automotive components such as engine parts, transmission components, and braking systems. The tight tolerances and high accuracy achieved through precision machining contribute to the performance and durability of vehicles.
4. Electronics industry: Precision machining is used in the manufacturing of electronic components such as connectors, housings, and PCBs. The precise dimensions and surface finishes achieved through machining ensure the functionality and reliability of electronic devices.
5. Tool and die making: Machining precision is essential in the production of tools and dies used in manufacturing processes. The accuracy and repeatability achieved through precision machining ensure the quality and consistency of machined parts.
Overall, machining precision is critical in various industries and applications where high accuracy, tight tolerances, and quality finishes are required. The use of advanced machining techniques and technologies allows manufacturers to achieve the desired precision levels and meet the stringent requirements of their customers.
Material of machining precision
Machining precision refers to the ability of a machine to produce parts with tight tolerances and accurate dimensions. The material used for machining plays a crucial role in achieving high precision.
One of the most common materials used for machining precision is steel. Steel is known for its durability and strength, making it ideal for producing precision parts that need to withstand harsh conditions. It also has good machinability, allowing for accurate cuts and shapes to be achieved.
Another material frequently used for machining precision is aluminum. Aluminum is a lightweight material that offers good corrosion resistance and excellent thermal conductivity. It is commonly used for applications that require tight tolerances and high precision, such as aerospace components and automotive parts.
Titanium is another material that is often used for machining precision. Titanium is known for its high strength-to-weight ratio, corrosion resistance, and biocompatibility. It is commonly used in industries such as medical, aerospace, and automotive, where high precision is required.
In addition to these materials, other metals such as copper, brass, and nickel alloys are also used for machining precision. Each material has its unique properties that make it suitable for specific applications where high precision is essential.
Overall, the material used for machining precision plays a vital role in achieving accurate and reliable parts. By selecting the right material based on the specific requirements of the application, manufacturers can ensure that their machined parts meet the desired specifications and quality standards.
Quality Testing Methods for machining precision and how to control the quality
There are several quality testing methods for machining precision that can be implemented to ensure the final product meets the desired specifications. Some of the commonly used methods include:
1. Dimensional measurement: This involves using calipers, micrometers, Coordinate Measuring Machines (CMM), or optical measurement devices to verify that the machined part’s dimensions meet the required tolerances.
2. Surface roughness measurement: Surface finish is critical in machining precision. Testing methods such as profilometers or surface roughness testers can be used to measure the surface roughness of the machined part.
3. Hardness testing: Hardness testing methods such as Rockwell or Vickers hardness tests can be used to determine the hardness of the material after machining. This is important to ensure the machined part can withstand the intended application.
4. Visual inspection: Visual inspection can be done to check for any visible defects, cracks, or surface irregularities on the machined part.
To control the quality of machining precision, it is important to have a comprehensive quality control plan in place. This may include implementing proper machining techniques, using calibrated tools, conducting regular maintenance on machines, and ensuring that operators are properly trained.
Additionally, monitoring and documenting the machining process, conducting regular quality checks throughout the production process, and implementing corrective actions if any deviations from the desired specifications are detected are essential steps to control the quality of machining precision.
Overall, implementing a combination of testing methods, rigorous quality control processes, and continuous improvement efforts can help ensure that the machined parts meet the required specifications for precision and quality.
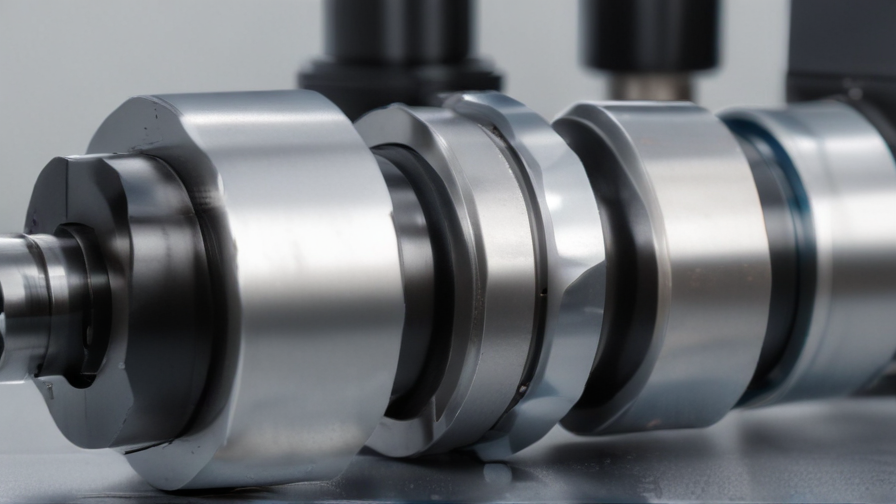
The Work Process and how to use machining precision
Machining precision is a critical factor in the work process as it ensures that the final product meets the required specifications and functions correctly. To achieve machining precision, the following steps are typically followed:
1. Planning: Before starting the machining process, it is essential to plan out the entire process, including selecting the right tools and materials, calculating the necessary dimensions, and determining the sequence of operations.
2. Setup: Once the planning is complete, the next step is to set up the machine tools and workpiece correctly. This includes securing the workpiece in place, aligning the cutting tool, and adjusting the speed and feed rate to achieve the desired precision.
3. Machining: With the setup complete, the machining process can begin. This involves using the cutting tool to remove material from the workpiece according to the planned dimensions. It is essential to monitor the process closely to ensure that the machining precision is maintained throughout.
4. Inspection: After the machining is complete, the final step is to inspect the finished product to ensure that it meets the required precision. This may involve using measuring tools like calipers or micrometers to check dimensions, or conducting tests to evaluate the functionality of the part.
In conclusion, machining precision is crucial in the work process to ensure that the final product meets the required specifications and functions correctly. By following the steps outlined above and paying close attention to detail throughout the process, machinists can achieve the desired level of precision in their work.
machining precision Importing questions including Cost,Supplier,Sample,Certification and Market
When importing precision machining products, there are several important questions to consider:
1. Cost: What is the cost of the machined products, including production costs and shipping fees? Are there any additional fees or taxes to consider?
2. Supplier: Who is the supplier of the precision machining products? Are they reputable and reliable? Do they have experience in the industry?
3. Sample: Can a sample of the machined products be provided before placing a larger order? This can help to ensure the quality and accuracy of the products.
4. Certification: Are the precision machining products certified to meet specific industry standards or regulations? This can be important for ensuring the products meet quality requirements.
5. Market: What is the market demand for the precision machining products? Are there potential competitors in the market? What is the sales potential for these products?
It is important to thoroughly research and evaluate potential suppliers and products before importing precision machining products. Working with a reputable supplier, obtaining samples for quality assurance, and ensuring certification and market potential can help to minimize risks and maximize success in importing precision machining products.
How to find and select check reliable machining precision manufacturers in China
When looking for reliable machining precision manufacturers in China, here are some steps to follow:
1. Research: Start by researching online for different machining precision manufacturers in China. Look for companies with a strong reputation, good reviews, and experience in the industry.
2. Verify credentials: Check if the manufacturer has the necessary certifications, such as ISO 9001, to ensure they meet quality standards.
3. Request samples: Ask for samples of their work to assess the quality of their products and services.
4. Check equipment and technology: Ensure that the manufacturer uses advanced machinery and technology for precision machining.
5. Visit the facility: If possible, visit the manufacturer’s facility to see their operation firsthand and assess their capabilities.
6. Request quotes: Get quotes from multiple manufacturers to compare prices and see if they fit your budget.
7. Check turnaround time: Inquire about their production lead times to ensure they can deliver your project within the required timeframe.
8. Communication: Communication is key in ensuring a successful partnership. Make sure the manufacturer is responsive and is able to address any concerns or questions.
By following these steps, you can find and select a reliable machining precision manufacturer in China that meets your requirements and standards.
Background Research for machining precision manufacturers Companies in China, use qcc.com archive.org importyeti.com
Machining precision manufacturers in China play a crucial role in supporting various industries, including automotive, aerospace, medical, and electronics. These companies use advanced technologies and equipment to produce high-quality components with tight tolerances and complex geometries.
QCC.com is a valuable resource for accessing information about machining precision manufacturers in China. The platform provides detailed profiles of companies, including their capabilities, certifications, and quality control processes. Users can also find customer reviews and ratings, helping them assess the credibility and reputation of potential suppliers.
Archive.org offers a wealth of historical data about machining precision manufacturers in China. By accessing archived websites and documents, users can track the evolution of companies over time, including changes in management, production processes, and market strategies. This information can be valuable for evaluating the long-term stability and reliability of suppliers.
Importyeti.com is a useful tool for researching the import and export activities of machining precision manufacturers in China. Users can find data on shipments, trade partners, and pricing trends, allowing them to identify emerging suppliers and monitor market dynamics. This information can be crucial for making informed decisions about sourcing components from Chinese manufacturers.
Overall, leveraging these platforms can provide valuable insights into the capabilities, reputation, and market dynamics of machining precision manufacturers in China, helping businesses identify reliable suppliers and optimize their supply chain strategies.
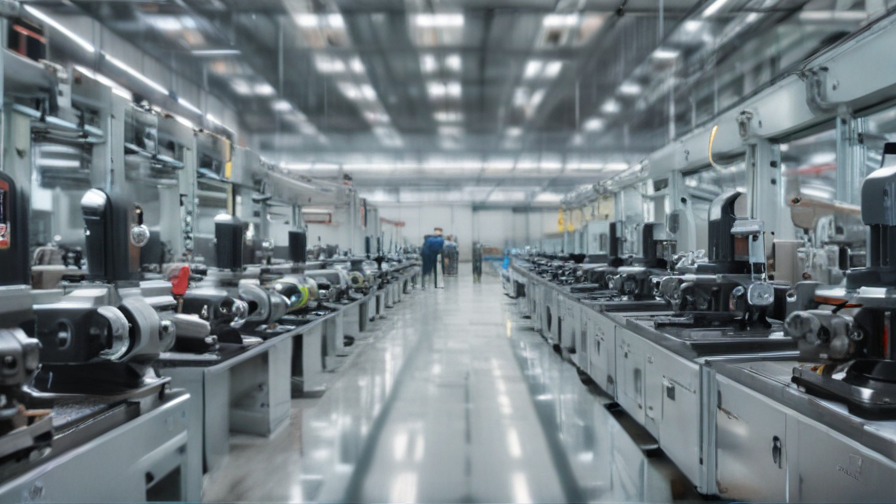
Price Cost Research for machining precision manufacturers Companies in China, use temu.com and 1688.com
When researching the pricing and cost of machining precision manufacturers in China, two popular websites to use are temu.com and 1688.com. These platforms provide access to a wide range of manufacturers and suppliers, making it easier to compare prices and find the best deals.
On temu.com, users can search for specific machining precision manufacturers and view their product offerings and pricing. Many manufacturers on this platform offer competitive pricing and high-quality products.
1688.com is another valuable resource for researching prices and costs for machining precision manufacturers in China. This platform allows users to directly communicate with suppliers, negotiate prices, and place orders. By using 1688.com, businesses can often find lower prices and better deals than other traditional sourcing methods.
When using these websites for price and cost research, it is important to compare multiple manufacturers and suppliers to ensure that you are getting the best value for your money. Additionally, be sure to factor in shipping costs, MOQ requirements, and any additional fees that may impact the overall cost.
Overall, temu.com and 1688.com are valuable tools for researching prices and costs for machining precision manufacturers in China. By utilizing these platforms, businesses can find the best deals and suppliers to meet their manufacturing needs.
Shipping Cost for machining precision import from China
When importing precision machining parts from China, it is important to consider the shipping cost as it can significantly impact the overall cost of the product. There are several factors that can affect the shipping cost, including the size and weight of the package, the shipping method, and the distance between the supplier in China and the destination.
One of the most common shipping methods for importing goods from China is sea freight, which is usually more cost-effective for large and heavy shipments. The cost of sea freight is calculated based on the volume and weight of the package, as well as the distance it needs to travel. Air freight, on the other hand, is faster but also more expensive than sea freight. The cost of air freight is typically based on the weight of the package, with higher rates for heavier shipments.
It is also important to consider additional costs such as insurance, customs duties, and taxes when calculating the total shipping cost. These costs can vary depending on the value of the goods being imported and the regulations of the importing country.
To keep the shipping cost within budget, it is advisable to compare quotes from different shipping companies and choose the most cost-effective option. Additionally, consolidating shipments or using a freight forwarder can help reduce costs by combining multiple orders into one shipment.
Overall, it is important to carefully consider the shipping cost when importing precision machining parts from China to ensure that the total cost remains within budget. By researching different shipping options and considering all additional costs, importers can optimize their supply chain and ensure a smooth and cost-effective import process.
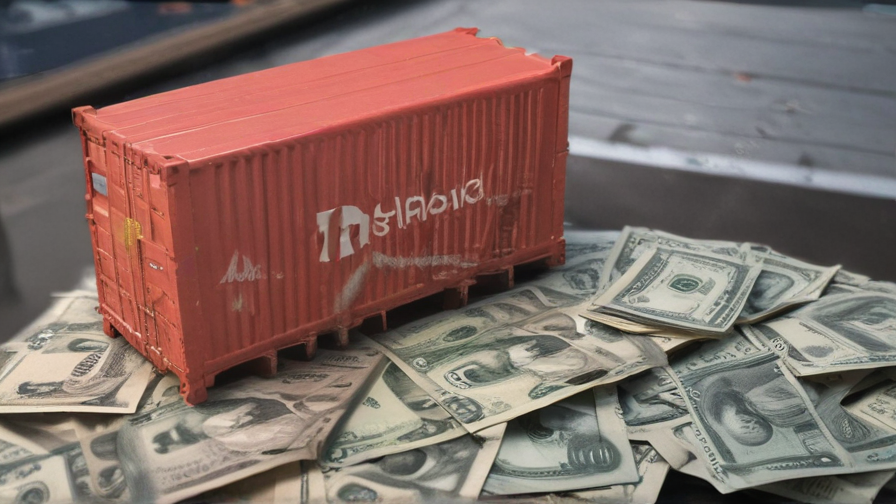
Compare China and Other machining precision Markets: Products Quality and Price,Visible and Hidden Costs
China is known for its competitive pricing in the machining precision market, offering relatively lower prices compared to other markets. However, this lower price often comes with concerns over product quality. Many companies in China may not adhere to the same rigorous quality control standards as other markets, leading to potential issues with precision and durability of products.
In terms of visible costs, China may appear as the more attractive option due to its cheaper labor and manufacturing expenses. However, there are often hidden costs associated with sourcing products from China, such as longer lead times, communication challenges, and potential quality control issues that may arise during production.
On the other hand, markets in countries like Japan, Germany, and the United States are known for their high-quality precision products. While these markets may have higher price points, the assurance of superior quality and reliability can offset the initial cost. The visible costs in these markets are typically higher due to more stringent quality control measures and skilled labor, but the reduced risk of defects and recalls may ultimately save costs in the long run.
In conclusion, while China may offer competitive pricing in the machining precision market, there are concerns regarding product quality and potential hidden costs. Other markets may have higher upfront costs but provide higher quality products with lower risks of defects. Companies must weigh these factors when choosing a supplier for machining precision products to ensure they are getting the best value for their investment.
Custom Private Labeling and Branding Opportunities with Chinese machining precision Manufacturers
Are you looking for custom private labeling and branding opportunities with Chinese machining precision manufacturers? Look no further! Our team of experienced professionals can help you take your products to the next level with personalized branding and packaging options.
By working with our network of trusted Chinese machining precision manufacturers, we can help you create a unique and memorable brand identity for your products. Whether you are looking to customize your packaging, add your logo to your products, or create a completely new brand design, our team can help make it happen.
We understand the importance of branding in today’s competitive marketplace, and we are dedicated to helping you stand out from the crowd. Our experienced team will work closely with you to develop a customized branding strategy that aligns with your company’s values and vision.
With our extensive network of Chinese machining precision manufacturers, we can ensure that your products are manufactured to the highest quality standards while also maintaining the integrity of your brand. Contact us today to learn more about how we can help you elevate your products with custom private labeling and branding opportunities.
Tips for Procurement and Considerations when Purchasing machining precision
When purchasing machining precision services, it is important to consider several factors to ensure you are getting the best value for your money. Here are some tips and considerations:
1. Supplier experience and expertise: Look for a supplier with a proven track record of delivering high-quality precision machining services. Check their references and ask for samples of their work.
2. Equipment and technology: Make sure the supplier has the necessary equipment and technology to meet your specific machining requirements. This includes CNC machining capabilities, as well as the ability to work with a wide range of materials.
3. Quality control measures: Inquire about the supplier’s quality control processes and certifications. A reputable supplier will have strict quality control measures in place to ensure the final product meets your specifications.
4. Turnaround time: Consider the supplier’s turnaround time and make sure they can meet your deadline. A quick turnaround time is important, especially for time-sensitive projects.
5. Pricing: Get quotes from multiple suppliers and compare prices to ensure you are getting a competitive rate. However, remember that the cheapest option may not always be the best in terms of quality and service.
6. Communication and customer service: Choose a supplier that is responsive and easy to communicate with. Good customer service is key to a successful partnership.
By considering these factors and following these tips, you can ensure that you are purchasing machining precision services that meet your specific requirements and deliver high-quality results.
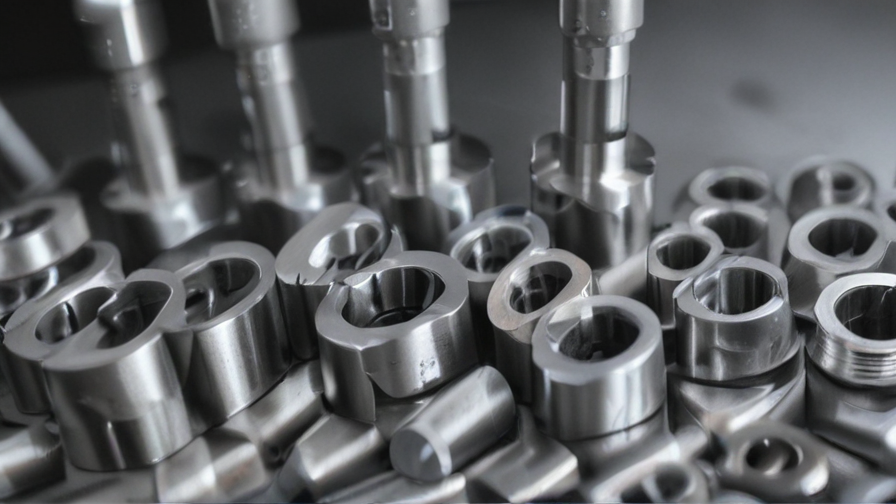
FAQs on Sourcing and Manufacturing machining precision in China
1. Why should I consider sourcing and manufacturing precision machining in China?
Sourcing and manufacturing precision machining in China can offer cost savings due to lower labor and production costs. China also has a large and skilled workforce, as well as access to advanced technology and equipment.
2. How can I find a reliable manufacturer for precision machining in China?
It is important to conduct thorough research and due diligence when looking for a manufacturer in China. Seek recommendations from industry contacts, attend trade shows, and visit manufacturing facilities in person to assess their capabilities and quality standards.
3. What are some common challenges of sourcing and manufacturing in China?
Some common challenges include language barriers, differences in business practices, quality control issues, and intellectual property concerns. It is essential to work with experienced sourcing agents or consultants to navigate these challenges effectively.
4. How can I ensure quality control when manufacturing precision machining in China?
Implementing strict quality control processes, conducting regular inspections and audits, and fostering open communication with the manufacturer are crucial steps to ensure the quality of your precision machining products.
5. Are there any regulations or certifications I need to be aware of when sourcing and manufacturing in China?
It is important to understand and comply with all relevant regulations and certifications for your specific industry and product requirements. Working with a reputable manufacturer that adheres to international quality standards can help ensure compliance and product integrity.
Why contact sourcifychina.com get free quota from reliable machining precision suppliers?
Sourcifychina.com offers a convenient and efficient platform for businesses to connect with reliable machining precision suppliers in China. By contacting Sourcify China, you can obtain a free quota from these reputable suppliers, allowing you to easily compare pricing, services, and capabilities before making a decision.
Accessing a free quota from Sourcify China’s network of machining precision suppliers can give you valuable insights into the cost and quality of their services, helping you make an informed decision when selecting a supplier for your machining needs. This service can save you time and resources by streamlining the supplier selection process and ensuring that you are working with trusted and reliable partners.
By using Sourcify China’s platform to obtain a free quota from machining precision suppliers, you can benefit from competitive pricing, high-quality services, and efficient communication throughout the sourcing and production process. This can help you streamline your supply chain and ensure the success of your machining projects.
Overall, contacting Sourcifychina.com to get a free quota from reliable machining precision suppliers is a smart and cost-effective way to find the right partners for your business. With their extensive network of trusted suppliers and convenient platform, Sourcify China can help you connect with the best machining precision suppliers in China to meet your specific needs.
Contact [email protected] Whatsapp 86 15951276160