Top Metal Forging Manufacturers Comprehensive Guide Sourcing from China.
Top metal forging in China introduce,list main products and website if have
China is home to some top metal forging companies that are known for their high quality products and advanced manufacturing processes. A few notable ones include:
1. China forging Inc. – this company specializes in the manufacturing of various forged metal products including gears, flanges, shafts, and other customized components for industries such as automotive, aerospace, and construction. Website: www.chinaforging.com
2. Dongguan Yuhua Forging Co., Ltd. – known for their expertise in hot forging, this company produces a wide range of metal components including connecting rods, crankshafts, and valve bodies. They serve industries such as automotive, machinery, and oil & gas. Website: www.yh-forge.com
3. GWO Forging – this company offers a diverse range of forged products such as flanges, rings, and bars for industries including marine, power generation, and defense. They are known for their extensive experience in forging complex and critical components. Website: www.gwoforging.com
4. Ningbo Hongsheng Forging Co., Ltd. – specializing in the production of forged parts for industries like automotive, agriculture, and hydraulic equipment. They offer a wide range of products including gears, sprockets, and drive shafts. Website: www.hongshengforging.com
These top metal forging companies in China are known for their commitment to quality, precision, and reliability in delivering forged metal products for various industries. With their advanced manufacturing processes and skilled workforce, they continue to be preferred suppliers for customers worldwide.
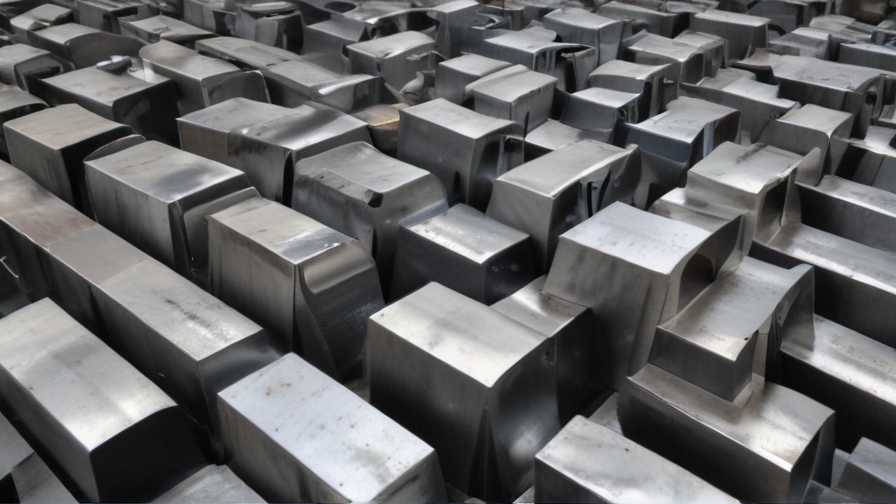
Types of metal forging
Metal forging is a manufacturing process in which a metal is shaped by applying localized compressive forces. There are several types of metal forging that are commonly used in industries:
1. Open-die forging: In this process, the metal is shaped between flat dies that do not enclose the workpiece entirely. The metal is hammered and shaped into the desired form by repeated blows from a hammer or press. Open-die forging is often used for large components such as shafts, rings, and discs.
2. Closed-die forging: Also known as impression-die forging, this process involves placing a metal workpiece between two dies that contain a precut cavity in the shape of the desired part. The metal is then forged into the cavity by applying high pressure. Closed-die forging is used to produce complex and detailed components such as gears, tools, and automotive parts.
3. Roll forging: In this forging process, a round bar of metal is shaped by passing it between two rollers that apply pressure to the material. The metal is gradually formed into the desired shape as it passes through the rollers. Roll forging is often used to produce long, cylindrical components such as shafts and axles.
4. Upset forging: This process involves shortening a metal workpiece by applying compressive forces to the ends. The metal is deformed and thickened at the ends, creating a larger cross-section. Upset forging is commonly used to produce items like bolts, rivets, and hammer heads.
5. Press forging: In this process, a metal workpiece is shaped by placing it between two dies and applying high pressure using a hydraulic or mechanical press. Press forging allows for precise control over the forging process and is often used to produce components with tight tolerances and complex shapes.
Overall, metal forging is a versatile manufacturing process that can be used to produce a wide range of components with varying sizes, shapes, and properties. Each type of forging method offers unique advantages and is chosen based on the specific requirements of the final product.
Pros and Cons of Using metal forging
Metal forging is a popular method used in the manufacturing industry to produce high-quality metal products. There are several pros and cons associated with using metal forging.
Pros of metal forging:
1. Strength and durability: Metal forging results in a product with increased strength and durability as the process compacts and shapes the metal grain structure, making it less prone to cracking or breaking.
2. Improved microstructure: The metal is reshaped and refined during forging, leading to a more uniform and refined microstructure, which enhances the mechanical properties of the metal.
3. Customizability: Metal forging allows for the production of a wide range of complex shapes and designs with high dimensional accuracy and consistency.
4. Cost-effectiveness: While the initial cost of metal forging equipment and tooling may be high, the long-term cost savings are significant due to the increased strength and durability of the forged products.
Cons of metal forging:
1. High initial cost: The cost of setting up metal forging equipment and tooling can be high, making it a significant investment for manufacturers.
2. Limited size and weight capacity: Metal forging is typically suited for producing smaller to medium-sized parts, and there may be limitations in terms of the size and weight of products that can be forged.
3. Time-consuming process: Metal forging is a time-consuming process as the metal needs to be heated, forged, cooled, and finished, which can result in longer production lead times compared to other manufacturing processes.
4. Environmental impact: Metal forging can have a high environmental impact due to the energy consumption required for heating the metal and the generation of waste materials, such as scale and excess metal.
In conclusion, metal forging offers several advantages in terms of strength, durability, customizability, and cost-effectiveness. However, it also has some drawbacks, such as high initial costs, limitations in size and weight capacity, time-consuming process, and environmental impact. It is essential for manufacturers to weigh the pros and cons of metal forging carefully before deciding to implement this manufacturing method.
metal forging Reference Specifications (varies for different product)
Metal forging is a manufacturing process in which a metal material is shaped and formed using compressive forces, typically applied through the use of a hammer or press. The process of forging metal results in an increase in strength, durability, and uniformity in the material.
There are various specifications that must be considered when forging metal, including the type of metal being used, the desired shape and size of the final product, and the level of precision required. For example, for a forged steel component, the reference specifications may include ASTM A668 for carbon steel forgings for general industrial use, ASTM A105 for carbon steel forgings for piping applications, or ASTM A182 for stainless steel forgings for high-temperature and pressure service.
The forging process involves heating the metal material to a specific temperature to make it more malleable, then shaping it using a die or mold to achieve the desired form. The forging process can be done using various techniques, such as open-die forging, closed-die forging, and impression-die forging, depending on the complexity and size of the final product.
After the metal has been forged, it may undergo additional processes such as heat treatment, surface finishing, and machining to achieve the desired properties and dimensions. Overall, metal forging is a versatile and important manufacturing process used to create strong and reliable metal components for various industries.
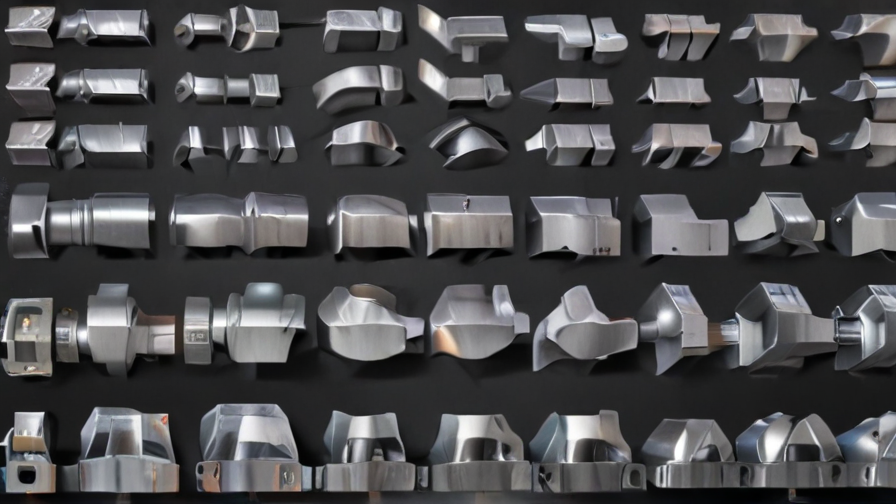
Applications of metal forging
Metal forging is a versatile process that has numerous applications across various industries. Some common applications of metal forging include the manufacturing of automotive parts, aerospace components, industrial machinery, and tools.
One of the key benefits of metal forging is its ability to produce parts with superior strength and durability. This makes it an ideal choice for critical components in the automotive industry, such as engine parts, suspension components, and transmission gears. Forging is also commonly used in the aerospace industry to produce high-strength components for aircraft engines, landing gear, and structural parts.
In the industrial machinery sector, metal forging is used to produce components such as gears, shafts, and valves. These parts require high strength and precision, making forging a preferred manufacturing method. Additionally, forging is commonly used in the production of hand tools, power tools, and agricultural equipment.
In the oil and gas industry, metal forging is used to produce components for drilling equipment, pipelines, and valves. These parts must withstand high temperatures, pressures, and corrosive environments, making forging an ideal manufacturing method.
Overall, metal forging offers a cost-effective and efficient way to produce high-quality, high-strength components for a wide range of industries. Its versatility, durability, and precision make it a popular choice for manufacturers looking to produce components that meet stringent quality standards.
Material of metal forging
Metal forging is a process in which a metal workpiece is compressed and deformed using localized compressive forces. There are several different materials that can be used for metal forging, with each material offering unique properties and advantages.
One of the most commonly used materials for metal forging is steel. Steel is a versatile and durable material that can be easily forged into a wide range of shapes and sizes. It is also known for its strength and toughness, making it a popular choice for applications where high performance is required.
Another popular material for metal forging is aluminum. Aluminum is lightweight and has excellent corrosion resistance, making it a good choice for applications where weight reduction is important. It is also highly formable, allowing it to be easily forged into complex shapes.
Other materials that are commonly used for metal forging include titanium, copper, and brass. Titanium is known for its high strength-to-weight ratio and corrosion resistance, making it a popular choice for aerospace and medical applications. Copper and brass are both highly malleable materials that are frequently used in decorative and ornamental forging applications.
In conclusion, there are a variety of materials that can be used for metal forging, with each material offering unique properties and advantages. Steel, aluminum, titanium, copper, and brass are just a few of the materials that can be forged to create high-quality and durable metal components. By carefully selecting the material that best fits the requirements of the application, manufacturers can produce forged metal parts that meet or exceed their customers’ expectations.
Quality Testing Methods for metal forging and how to control the quality
Metal forging quality can be ensured through various testing methods such as visual inspection, non-destructive testing, and mechanical testing. Visual inspection involves examining the forged metal for any surface defects or irregularities. Non-destructive testing techniques like ultrasonic testing, magnetic particle testing, and liquid penetrant testing can be used to detect internal defects without damaging the material. Mechanical testing involves evaluating the mechanical properties of the forged metal, such as tensile strength, hardness, and impact resistance.
To control the quality of metal forging, it is essential to establish stringent quality control processes at every stage of the manufacturing process. This includes ensuring that only high-quality raw materials are used, maintaining proper forging temperatures and pressures, and closely monitoring the forging process to prevent defects. Regular training and certification of forging operators can also help ensure consistency and quality in the final product.
Additionally, implementing a quality management system, such as ISO 9001, can help ensure that all quality control measures are being followed and that any issues are promptly addressed. Continuous improvement strategies, such as implementing lean manufacturing principles and conducting regular audits and reviews, can help identify areas for improvement and prevent quality issues from occurring in the future.
By incorporating these testing methods and quality control measures into the metal forging process, manufacturers can produce high-quality forged products that meet or exceed customer expectations. This not only helps maintain a positive reputation in the industry but also ensures the safety and reliability of the final product.
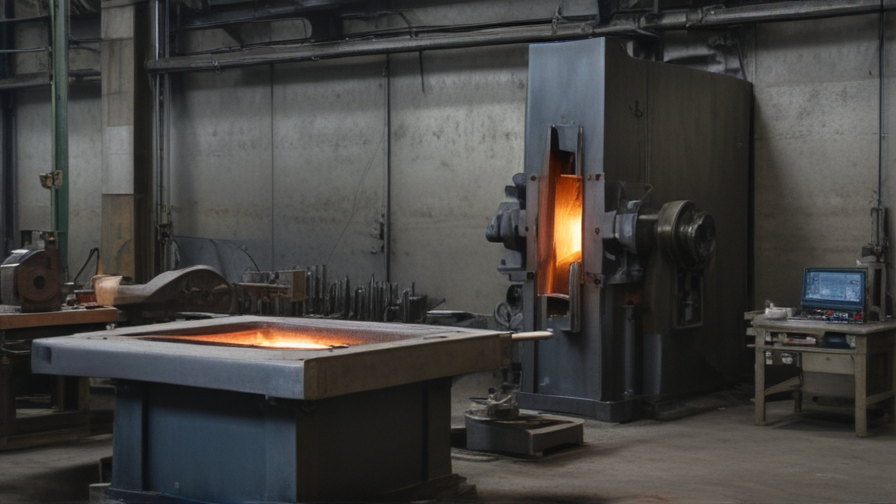
The Work Process and how to use metal forging
Metal forging is a manufacturing process where metal is shaped through the application of compressive forces. The process involves heating a metal to a high temperature and then hammering or pressing it into the desired shape. Here is a general overview of the metal forging process:
1. Heating: The first step in metal forging is heating the metal to a temperature where it becomes malleable. The exact temperature will vary depending on the type of metal being used.
2. Shaping: Once the metal has reached the correct temperature, it is placed on a die or anvil and hammered or pressed into the desired shape. This can be done manually or using a mechanical or hydraulic press.
3. Cooling: After shaping, the metal is allowed to cool gradually to room temperature. This annealing process helps to strengthen the metal and relieve any internal stresses.
4. Finishing: Once the metal has cooled, it may be further shaped or machined to achieve the final desired dimensions and surface finish.
Metal forging has several advantages over other manufacturing processes, including improved strength, better grain structure, and enhanced durability. It is commonly used in industries such as automotive, aerospace, and construction.
To use metal forging effectively, it is essential to have the right equipment and a skilled workforce. The process requires specialized tools, such as hammers, presses, and dies, as well as knowledge of the metallurgical properties of the metals being used.
In conclusion, metal forging is a versatile and efficient manufacturing process that can produce high-quality, durable metal components. By understanding the work process and following best practices, manufacturers can leverage the benefits of metal forging to create superior products.
metal forging Importing questions including Cost,Supplier,Sample,Certification and Market
When considering importing metal forging products, there are several key questions to keep in mind.
Firstly, what is the cost of the metal forging products from the supplier? It is important to ensure that the cost is competitive and aligns with your budget and pricing strategy.
Secondly, who is the supplier of the metal forging products? It is crucial to choose a reliable and reputable supplier with a track record of delivering high-quality products on time.
Thirdly, can you request a sample of the metal forging products before placing a bulk order? Sampling allows you to assess the quality and suitability of the products for your business.
Fourthly, what certifications does the supplier have for their metal forging products? Certifications such as ISO, CE, or RoHS can demonstrate the quality and compliance of the products.
Lastly, what is the market demand for metal forging products in your target market? Conducting market research can help you determine the potential demand and competition in the market.
Overall, by carefully considering these questions and conducting due diligence, you can make informed decisions when importing metal forging products for your business.
How to find and select check reliable metal forging manufacturers in China
To find and select reliable metal forging manufacturers in China, start by researching online to identify potential companies. Look for manufacturers with a strong reputation, positive customer reviews, and a history of supplying high-quality products. Websites like Alibaba, Made-in-China, and Global Sources are good platforms to search for suppliers.
Next, contact the manufacturers directly to inquire about their experience, capabilities, production processes, quality control measures, and certifications. Ask for samples of their work, as well as references from past clients. Consider conducting a factory visit to assess their facilities and ensure they meet your standards.
When selecting a manufacturer, prioritize those with the necessary expertise and equipment to meet your specific forging requirements. Look for companies with experience in your industry or with similar projects. Make sure they can handle the volume of production you require and have a track record of delivering on time.
Lastly, negotiate terms and pricing with the selected manufacturer to ensure they are aligned with your budget and timeline. Make sure to have a clear agreement in place outlining all expectations and requirements to avoid any misunderstandings down the line.
Overall, due diligence and thorough research are key to finding a reliable metal forging manufacturer in China. By following these steps and carefully vetting potential suppliers, you can ensure a successful partnership and high-quality products.
Background Research for metal forging manufacturers Companies in China, use qcc.com archive.org importyeti.com
Metal forging is a common manufacturing process in China, with many companies specializing in this technique. Some notable metal forging manufacturers in China include Xinghua Dongchang Alloy Steel Co., Ltd., Jianfeng Group, and Dalian Huarui Heavy Industry Group Co., Ltd.
Xinghua Dongchang Alloy Steel Co., Ltd. is a leading manufacturer of forging products in China, specializing in the production of alloy steel. The company has a strong reputation for high-quality products and reliable customer service.
Jianfeng Group is another prominent metal forging manufacturer in China, offering a wide range of forged products for industries such as automotive, aerospace, and energy. The company has a well-established presence in the market and is known for its advanced manufacturing techniques and efficient production processes.
Dalian Huarui Heavy Industry Group Co., Ltd. is a key player in the metal forging industry in China, with a focus on heavy industrial components. The company has a large production capacity and is known for its ability to handle complex and large-scale forging projects.
Overall, metal forging manufacturers in China have a strong reputation for producing high-quality products and are capable of meeting the demands of various industries. With advanced manufacturing techniques and a focus on customer satisfaction, these companies continue to thrive in the competitive global market.
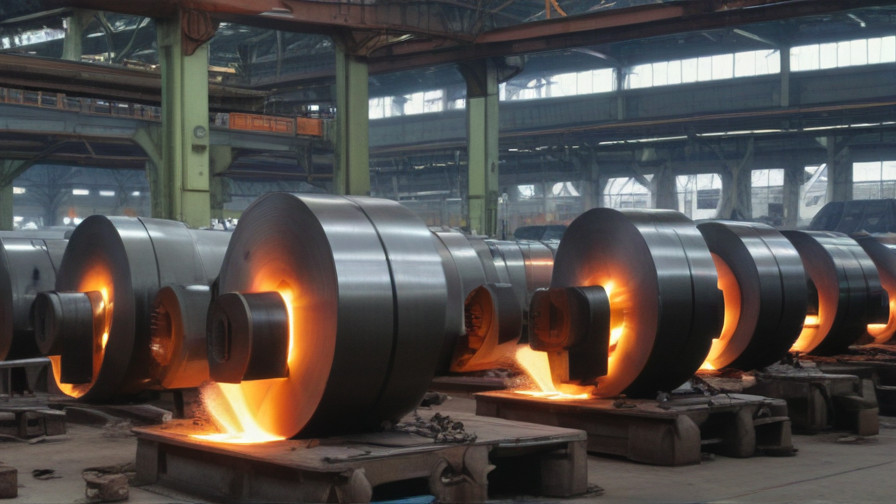
Price Cost Research for metal forging manufacturers Companies in China, use temu.com and 1688.com
When it comes to researching prices and costs for metal forging manufacturers in China, two popular websites to use are temu.com and 1688.com. These platforms provide access to a wide range of suppliers and manufacturers, making it easier to compare prices and find the best deals.
On temu.com, you can browse through a variety of metal forging manufacturers in China and view their product offerings and pricing. This platform allows you to directly contact the manufacturers for more information or to request a quote. Additionally, temu.com offers reviews and ratings from other buyers, helping you to choose the most reputable and reliable suppliers.
1688.com is another useful website for researching prices and costs for metal forging manufacturers in China. This platform, similar to Alibaba, provides access to a large number of suppliers and manufacturers, allowing you to easily compare prices and products. 1688.com also offers features such as customer reviews and ratings, helping you to make informed decisions when choosing a supplier.
By utilizing these two websites, you can efficiently research prices and costs for metal forging manufacturers in China. With access to a wide range of suppliers and manufacturers, you can find the best deals and make informed purchasing decisions for your business.
Shipping Cost for metal forging import from China
The shipping cost for importing metal forging from China will vary depending on several factors such as the weight, size, and quantity of the items being shipped. Generally, the cost can range from a few hundred dollars to several thousand dollars.
If you are importing a large quantity of metal forgings, it is recommended to use sea freight as it is more cost-effective compared to air freight. The cost of sea freight will depend on the volume and weight of the shipment, as well as the distance between the origin and destination ports.
For smaller quantities or urgent shipments, air freight may be a better option despite being more expensive. The cost of air freight is usually calculated based on the weight or volume of the shipment, whichever is higher.
In addition to the shipping method, other factors that can affect the cost of importing metal forgings from China include customs duties, taxes, insurance, and handling fees. It is advisable to work with a reputable freight forwarder or customs broker who can provide a breakdown of all associated costs and help you navigate the import process smoothly.
Overall, it is important to consider all the factors mentioned above and obtain quotes from multiple shipping providers to find the most cost-effective and reliable option for importing metal forgings from China.
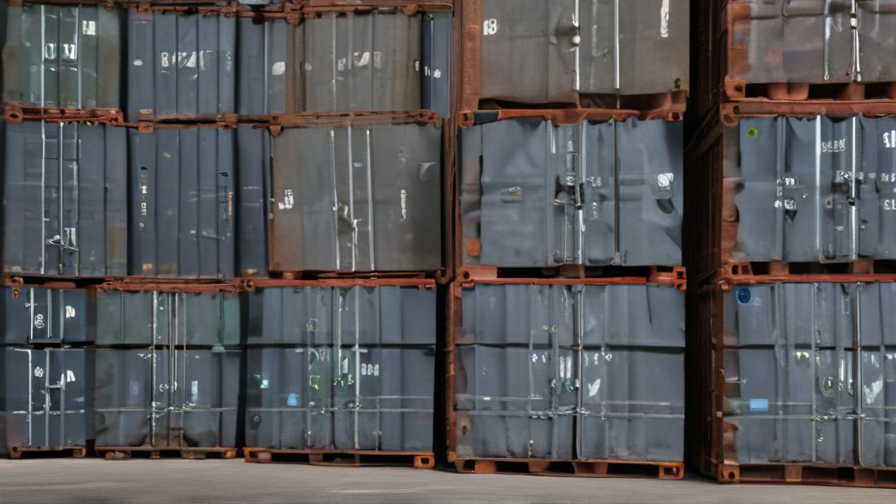
Compare China and Other metal forging Markets: Products Quality and Price,Visible and Hidden Costs
China is known for its massive production capacity and low labor costs, making it a dominant player in the metal forging market. The products from China typically have competitive prices, but the quality can vary depending on the supplier. While some Chinese manufacturers offer high-quality products that meet international standards, others may cut corners to keep costs low, resulting in lower quality products.
On the other hand, metal forging markets in countries like the United States, Germany, and Japan are known for their high-quality products. The products from these markets are often manufactured using advanced technology and strict quality control measures, ensuring superior performance and durability. However, this higher quality often comes at a correspondingly higher price compared to Chinese products.
In terms of visible and hidden costs, Chinese products may come with lower upfront prices, but there could be hidden costs associated with quality control issues, shipping delays, and inconsistent product performance. On the other hand, products from markets like the US, Germany, and Japan may have higher upfront prices, but they often come with better quality assurance, lower defect rates, and reliable delivery times, ultimately reducing the risk of hidden costs.
Overall, while China offers competitive pricing and a vast array of products in the metal forging market, buyers should carefully consider the trade-offs between price and quality. Markets like the US, Germany, and Japan may have higher price points, but they offer superior product quality and lower risks of hidden costs in the long run.
Custom Private Labeling and Branding Opportunities with Chinese metal forging Manufacturers
Chinese metal forging manufacturers offer custom private labeling and branding opportunities for businesses looking to create their own unique products. By partnering with a Chinese manufacturer, companies can take advantage of cost-effective production while still maintaining control over their brand identity.
With private labeling, businesses can personalize products with their own logos, designs, and branding elements. This allows companies to create exclusive products that stand out in the market and build brand loyalty among customers. By working with a Chinese manufacturer, businesses can access a wide range of forging capabilities and materials to create high-quality products that meet their specific requirements.
In addition to private labeling, Chinese manufacturers also offer branding opportunities for businesses looking to establish a distinct identity in the marketplace. By working closely with manufacturers on product development and design, companies can create unique products that reflect their brand values and messaging. This can help businesses differentiate themselves from competitors and attract new customers.
Overall, partnering with Chinese metal forging manufacturers for private labeling and branding opportunities can provide businesses with a competitive edge in the market. With access to cost-effective production and a wide range of capabilities, companies can create custom products that resonate with their target audience and help drive business growth.
Tips for Procurement and Considerations when Purchasing metal forging
When procuring metal forging, there are several factors to consider in order to make a successful purchase. Here are some tips and considerations to keep in mind:
1. Quality: Ensure that the metal forging meets your quality standards and requirements. Look for suppliers who have a good reputation for producing high-quality forgings that meet industry standards.
2. Material: Consider the type of metal that is most suitable for your specific application. Different metals have different properties and strengths, so it is important to choose the right material for your needs.
3. Cost: Compare prices from different suppliers to get the best value for your money. However, be cautious of extremely low prices, as this could indicate lower quality forgings.
4. Lead time: Consider the lead time for manufacturing and delivery of the metal forgings. Make sure the supplier can meet your timeline requirements to avoid delays in your production schedule.
5. Capacity: Ensure that the supplier has the capacity to produce the quantity of metal forgings that you need. Check their production capabilities and equipment to ensure they can fulfill your order.
6. Certification: Look for suppliers who are certified and comply with industry standards and regulations. This can ensure that the metal forgings meet quality and safety requirements.
7. Communication: Establish good communication with the supplier to ensure that your requirements are clearly understood and met. This can help prevent misunderstandings and ensure a successful procurement process.
By keeping these tips and considerations in mind, you can make a well-informed decision when purchasing metal forgings for your business needs.
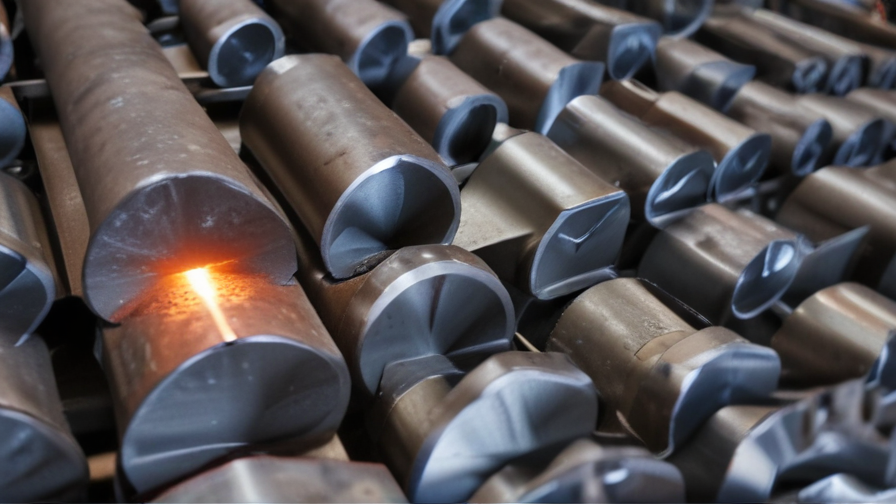
FAQs on Sourcing and Manufacturing metal forging in China
Q: What factors should I consider when sourcing metal forging in China?
A: When sourcing metal forging in China, it is important to consider factors such as the supplier’s experience and reputation, quality control processes, production capacity, pricing, and communication capabilities. Additionally, you should also ensure that the supplier complies with international standards and regulations to guarantee product quality and safety.
Q: What are the advantages of manufacturing metal forging in China?
A: Some of the advantages of manufacturing metal forging in China include cost savings due to lower labor and production costs, access to a large pool of skilled labor and advanced manufacturing technology, quick turnaround times, and the ability to produce large quantities of forgings efficiently. Additionally, China has a well-established supply chain network that can support the production process effectively.
Q: How can I ensure quality control when manufacturing metal forging in China?
A: To ensure quality control when manufacturing metal forging in China, you should conduct thorough supplier evaluations, perform regular inspections and audits of the production process, and communicate clearly with the supplier to set quality standards and expectations. Additionally, you can also work with third-party quality assurance companies to monitor and verify the production process to ensure that the forgings meet your specifications and requirements.
Why contact sourcifychina.com get free quota from reliable metal forging suppliers?
Sourcifychina.com is a trusted platform that connects businesses with reliable metal forging suppliers in China. By contacting Sourcifychina.com, you can get a free quota from multiple reputable suppliers without having to spend time and resources searching for them yourself. This will save you the hassle of vetting potential suppliers and ensure that you are getting the best quality products at competitive prices.
Using Sourcifychina.com to obtain a free quota from reliable metal forging suppliers will also give you access to a wide selection of suppliers that have been thoroughly vetted by the platform. This means that you can trust that the suppliers you are working with are reputable, experienced, and capable of meeting your specific requirements.
By utilizing Sourcifychina.com, you can streamline the sourcing process and save valuable time and resources that can be better spent on other aspects of your business. Additionally, you can benefit from the platform’s expertise in matching businesses with the right suppliers, ensuring a smooth and efficient sourcing experience.
Overall, contacting Sourcifychina.com to get a free quota from reliable metal forging suppliers is a smart and efficient way to source high-quality products from trusted suppliers in China.
Contact [email protected] Whatsapp 86 15951276160