Contents of Table
Top Plastic Part Manufacturing Manufacturers Comprehensive Guide Sourcing from China.
Top plastic part manufacturing in China introduce,list main products and website if have
One of the top plastic part manufacturers in China is TCL Mould. They specialize in creating high-quality plastic injection molds and parts for a variety of industries including automotive, electronics, and household appliances. Some of their main products include automotive interior and exterior parts, medical device components, and consumer electronics enclosures.
Another top plastic part manufacturer in China is Shenzhen Sunmy Hardware Co., Ltd. They offer a wide range of plastic parts such as injection molded components, CNC machined parts, and sheet metal parts. Their main products include electronic enclosures, plastic gears, and custom plastic prototypes.
For a more comprehensive list of plastic part manufacturers in China, you can visit websites such as Alibaba.com or Made-in-China.com. These platforms feature a wide range of manufacturers offering various plastic parts such as injection molding, blow molding, and extrusion products.
It is important to conduct thorough research and due diligence when selecting a plastic part manufacturer in China to ensure the quality and reliability of the products. Make sure to request samples, review the manufacturer’s certifications and quality control processes, and consider factors such as lead time, pricing, and communication before making a decision.
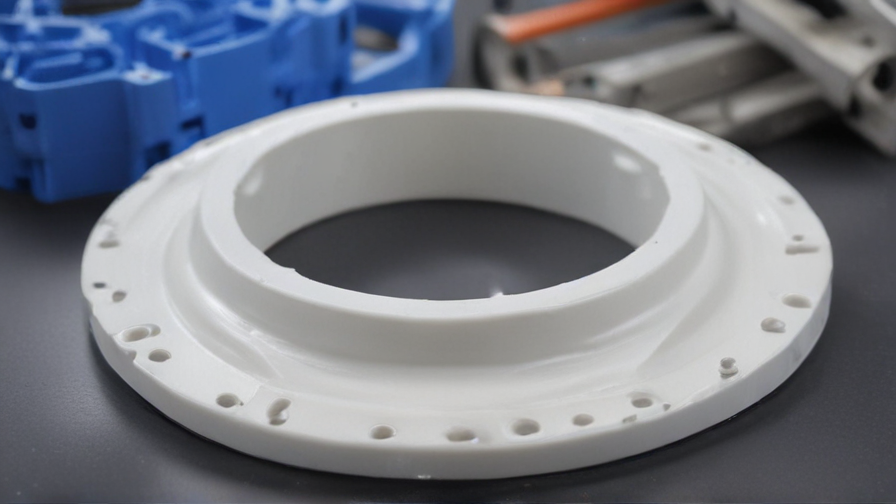
Types of plastic part manufacturing
Plastic part manufacturing involves various processes that can be categorized into different types based on the production methods and technologies used. Some common types of plastic part manufacturing include injection molding, blow molding, thermoforming, and rotational molding.
Injection molding is the most widely used method for producing plastic parts. It involves melting plastic resin and injecting it into a mold to form the desired shape. This process is suitable for high volume production and can produce complex geometries with high precision.
Blow molding is another common technique used to produce hollow plastic parts such as bottles and containers. In this process, molten plastic is extruded into a parison (hollow tube) and then inflated into a mold to create the final shape.
Thermoforming is a manufacturing method where a plastic sheet is heated and formed into a specific shape using a mold. This process is often used for producing packaging trays, clamshells, and disposable cups.
Rotational molding, also known as rotomolding, involves rotating a mold while heating and cooling plastic resin to create hollow parts such as tanks, containers, and playground equipment. This process allows for the production of large, seamless, and durable products.
Other types of plastic part manufacturing include compression molding, extrusion molding, and vacuum forming, each with its own advantages and applications. Different processes are chosen based on factors such as part complexity, production volume, cost considerations, and material properties. By carefully selecting the appropriate manufacturing method, manufacturers can achieve high-quality plastic parts that meet the specific requirements of their application.
Pros and Cons of Using plastic part manufacturing
Plastic part manufacturing has several advantages, such as affordability, versatility, and durability. Plastic parts are generally less expensive to manufacture compared to metal or other materials, making it a cost-effective option for businesses. Additionally, plastic materials can be easily molded into different shapes and sizes, allowing for greater design flexibility and customization. Plastic parts are also lightweight, making them ideal for industries where weight is a concern.
However, there are also some drawbacks to using plastic part manufacturing. One of the major concerns is environmental impact. Plastic is a non-biodegradable material, meaning it can take hundreds of years to decompose, leading to pollution and harm to wildlife. Additionally, plastic manufacturing processes can release harmful chemicals and greenhouse gases into the environment. Another downside is that plastic parts may not be as strong or durable as metal counterparts, making them more prone to wear and tear over time.
In conclusion, while plastic part manufacturing offers many benefits, it is important to consider the environmental implications and long-term durability when choosing this option. Businesses should weigh the pros and cons carefully and consider implementing sustainable practices to minimize the negative impact of plastic manufacturing.
plastic part manufacturing Reference Specifications (varies for different product)
Plastic parts manufacturing requires adherence to various reference specifications that may vary depending on the specific product being produced. Some common reference specifications include ASTM D7291 for molding and extrusion of plastic materials, ASTM D6103 for injection molding of thermoplastic materials, and ASTM D5989 for testing the tensile properties of plastics.
In addition to ASTM standards, manufacturers may also need to follow specific industry guidelines and customer requirements when producing plastic parts. These guidelines may dictate the material selection, molding process, dimensional tolerances, surface finish requirements, and testing procedures for ensuring product quality and performance.
Manufacturers must carefully select the appropriate raw materials based on the desired mechanical, thermal, and chemical properties of the end product. They must also ensure that the molding process, whether it be injection molding, blow molding, or extrusion, is carried out according to approved procedures and parameters to achieve the desired shape and properties of the plastic part.
Quality control measures, such as regular testing and inspection of finished parts, are essential to ensure that they meet the specified requirements and perform as intended. Manufacturers must also consider factors such as environmental impact, regulatory compliance, and overall cost-effectiveness in their plastic part manufacturing processes.
By closely adhering to reference specifications, industry guidelines, and customer requirements, manufacturers can produce high-quality plastic parts that meet the necessary standards and satisfy customer expectations.
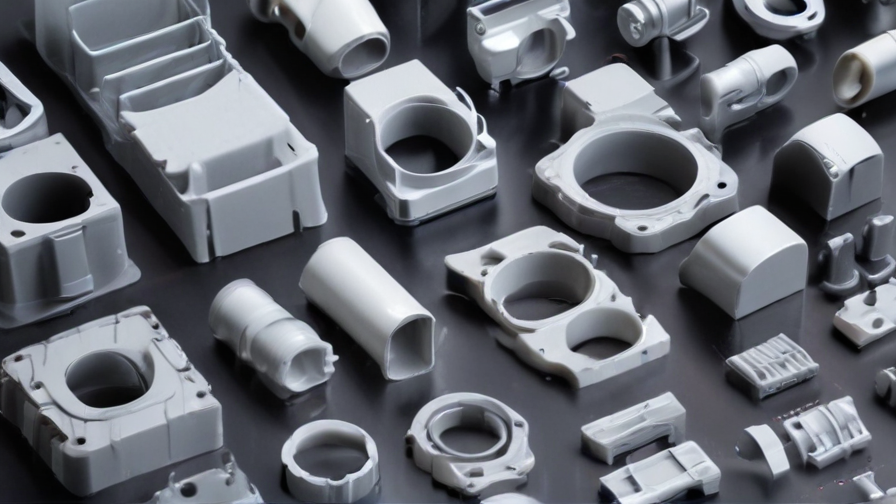
Applications of plastic part manufacturing
Plastic part manufacturing plays a crucial role in various industries, including automotive, aerospace, medical, and consumer goods. One of the most common applications of plastic part manufacturing is in the automotive industry, where plastic parts are used in the manufacturing of interior and exterior components such as bumpers, trim pieces, and dashboard components. Plastic parts are preferred in the automotive industry due to their durability, lightweight, and cost-effectiveness.
In the aerospace industry, plastic parts are used in the manufacturing of components such as ducts, panels, and interior fixtures. Plastic parts are preferred in aerospace applications due to their ability to withstand high temperatures and harsh environmental conditions. The lightweight nature of plastic parts also contributes to improved fuel efficiency in aircraft.
In the medical industry, plastic parts are used in the manufacturing of medical devices such as syringes, IV tubing, and surgical instruments. Plastic parts are preferred in medical applications due to their biocompatibility, sterilizability, and ease of manufacturing complex shapes.
In the consumer goods industry, plastic parts are used in the manufacturing of a wide range of products, including electronics, toys, and household appliances. Plastic parts are preferred in consumer goods applications due to their versatility, aesthetic appeal, and cost-effectiveness.
Overall, plastic part manufacturing plays a crucial role in various industries due to its versatility, cost-effectiveness, and ability to meet the specific requirements of different applications. The use of plastic parts continues to expand as new technologies and materials are developed, making them an essential component of modern manufacturing processes.
Material of plastic part manufacturing
There are several methods for manufacturing plastic parts, with each method offering its own set of advantages and disadvantages.
Injection molding is the most commonly used method for producing plastic parts. It involves melting plastic pellets and then injecting the molten plastic into a mold cavity. Once the plastic has cooled and solidified, the mold is opened and the part is ejected. Injection molding is fast, efficient, and can produce large quantities of parts with high precision.
Extrusion is another common method for manufacturing plastic parts. In extrusion, plastic pellets are melted and forced through a die to create a continuous shape, such as a tube or pipe. The plastic is then cooled and cut to the desired length. Extrusion is a cost-effective method for producing long, continuous parts with a consistent cross-section.
Thermoforming is a process in which a sheet of plastic is heated until pliable and then formed over a mold using vacuum pressure or compressed air. Once the plastic has cooled and hardened, the part is trimmed to its final shape. Thermoforming is ideal for producing large, shallow parts with complex geometries.
Blow molding is a method for producing hollow plastic parts, such as bottles or containers. In blow molding, a hollow tube of plastic, called a parison, is placed in a mold cavity and inflated with air to take on the shape of the mold. Once the plastic has cooled and solidified, the mold is opened, and the part is removed.
Overall, the choice of manufacturing method for plastic parts will depend on factors such as the desired part geometry, production volume, and material properties. Each method offers its own set of advantages and limitations, so it is important to carefully consider these factors when selecting a manufacturing process.
Quality Testing Methods for plastic part manufacturing and how to control the quality
Quality testing methods for plastic part manufacturing include visual inspection, dimensional analysis, mechanical testing, and material analysis. Visual inspection involves examining the part for any surface defects or imperfections, while dimensional analysis ensures that the part meets the specified dimensions and tolerances.
Mechanical testing includes tests such as tensile strength, impact resistance, and hardness testing to evaluate the mechanical properties of the plastic part. Material analysis involves testing the composition and properties of the plastic material used in the part to ensure it meets the required standards.
To control the quality of plastic parts, it is important to establish a comprehensive quality control process that incorporates these testing methods at various stages of manufacturing. This process should include regular inspection and testing of raw materials, in-process testing during manufacturing, and final inspection of finished parts.
Additionally, implementing a quality management system such as ISO 9001 can help ensure consistency and reliability in the manufacturing process. Training employees on quality standards and procedures, maintaining accurate documentation, and implementing corrective and preventive actions when defects are found are also essential to controlling quality.
By using these testing methods and implementing a robust quality control process, manufacturers can ensure that plastic parts meet the necessary requirements and specifications, resulting in high-quality and reliable products.
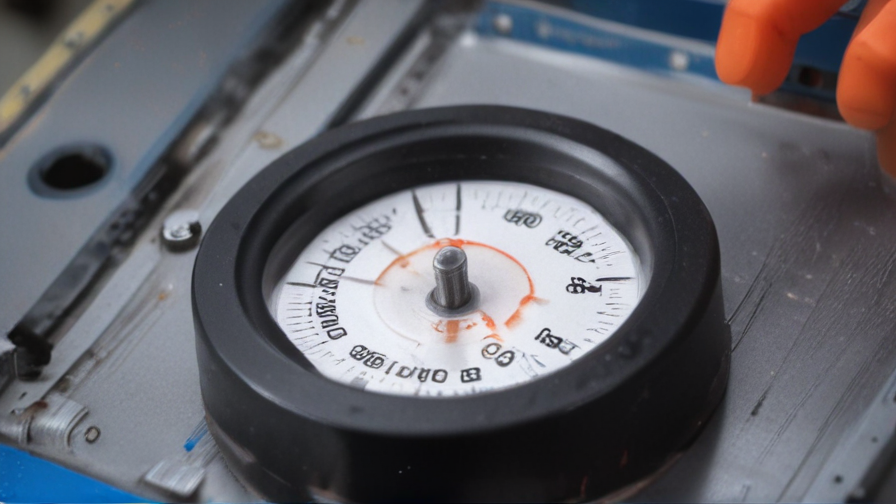
The Work Process and how to use plastic part manufacturing
Plastic part manufacturing is a complex process that involves several steps to successfully produce high-quality plastic parts. The work process typically involves the following steps:
1. Design: The first step in plastic part manufacturing is to design the product. This involves creating detailed drawings or computer-aided design (CAD) models of the part to be manufactured.
2. Material selection: Once the design is finalized, the next step is to select the appropriate plastic material for the part. Factors such as strength, durability, and cost must be considered when choosing the material.
3. Tooling: After selecting the material, molds or dies are created to shape the plastic material into the desired part. These tools are typically made from steel and are precision machined to ensure accuracy and consistency in the manufacturing process.
4. Injection molding: The most common method of plastic part manufacturing is injection molding. In this process, the plastic material is heated to a liquid state and injected into the mold under high pressure. Once the material cools and solidifies, the part is ejected from the mold.
5. Finishing: After the part is removed from the mold, any excess material or rough edges are trimmed or machined to achieve the final desired shape and finish.
To effectively utilize plastic part manufacturing, it is essential to follow these steps and use proper equipment and techniques. It is also important to work with experienced manufacturers who have the expertise and resources to produce high-quality plastic parts efficiently.
In conclusion, plastic part manufacturing is a multi-step process that requires careful planning, design, and execution. By following the work process outlined above and working with reliable manufacturers, businesses can produce plastic parts that meet their specific requirements in a cost-effective and timely manner.
plastic part manufacturing Importing questions including Cost,Supplier,Sample,Certification and Market
When importing plastic parts for manufacturing, there are several key questions to consider. Firstly, what is the cost of the parts from the supplier? It’s important to compare quotes from different suppliers to ensure you are getting the best price without compromising on quality.
Secondly, it’s crucial to assess the reliability and reputation of the supplier. This includes checking their track record, production capacity, and quality control processes. Requesting samples of the plastic parts before placing a bulk order is also advisable to physically inspect the product and ensure it meets your specifications.
Furthermore, inquire about the certification of the supplier and the plastic parts. It’s essential to ensure that the parts meet industry standards and regulatory requirements. Certifications such as ISO 9001 can provide assurance of quality and compliance.
Lastly, consider the market for the plastic parts. Research the demand for your products in the target market and assess potential competitors. Understanding market trends and consumer preferences will help you make informed decisions about importing plastic parts for manufacturing. By carefully considering these factors, you can ensure a successful and cost-effective import process for your plastic part manufacturing needs.
How to find and select check reliable plastic part manufacturing manufacturers in China
When looking for reliable plastic part manufacturing manufacturers in China, there are several key factors to consider.
1. Research: Start by researching and compiling a list of potential manufacturers. You can use online B2B platforms like Alibaba, Made-in-China, or Global Sources to find a variety of suppliers. Look for manufacturers with a good reputation, experience in the industry, and positive customer reviews.
2. Verify credentials: Check for certifications such as ISO 9001, ISO 14001, or other relevant quality management standards. This indicates that the manufacturer follows strict quality control procedures.
3. Request samples: Ask for samples of the plastic parts you are looking to manufacture. This will allow you to assess the quality of their products firsthand.
4. Communication: Reach out to the manufacturers and ask them about their production processes, pricing, lead times, and any other relevant information. Good communication is key to establishing a successful partnership.
5. Visit the factory: If possible, consider visiting the manufacturer’s factory to see their facilities and meet their team in person. This will give you a better idea of their capabilities and quality standards.
6. Get quotes: Request quotes from multiple manufacturers and compare them based on factors like pricing, quality, lead times, and communication. Choose a manufacturer that offers a good balance of quality and affordability.
By following these steps, you can find and select a reliable plastic part manufacturing manufacturer in China that meets your requirements and expectations.
Background Research for plastic part manufacturing manufacturers Companies in China, use qcc.com archive.org importyeti.com
China is one of the leading countries in the world when it comes to plastic part manufacturing. Companies in China that are involved in plastic part manufacturing include:
– Dongguan Jishun Plastic Products Co., Ltd. which specializes in the production of plastic parts for various industries such as automotive, electronics, and household products. They have a strong focus on quality control and use advanced technology in their manufacturing processes.
– Ningbo HPM Global Trading Co., Ltd. is another major player in the plastic part manufacturing industry in China. They offer a wide range of plastic parts for industries such as automotive, medical, and consumer goods. They are known for their high-quality products and efficient production processes.
– Shenzhen RJC Industrial Co., Ltd. is a company that specializes in custom plastic part manufacturing. They have a team of experienced engineers and designers who work closely with clients to develop custom plastic parts that meet their specific requirements. They have a strong reputation for delivering high-quality products in a timely manner.
Overall, companies in China that are involved in plastic part manufacturing have a strong focus on quality control, advanced technology, and customization options for their clients. By utilizing platforms such as qcc.com, archive.org, and importyeti.com, one can gain valuable insights into these companies and their capabilities in the plastic part manufacturing industry.
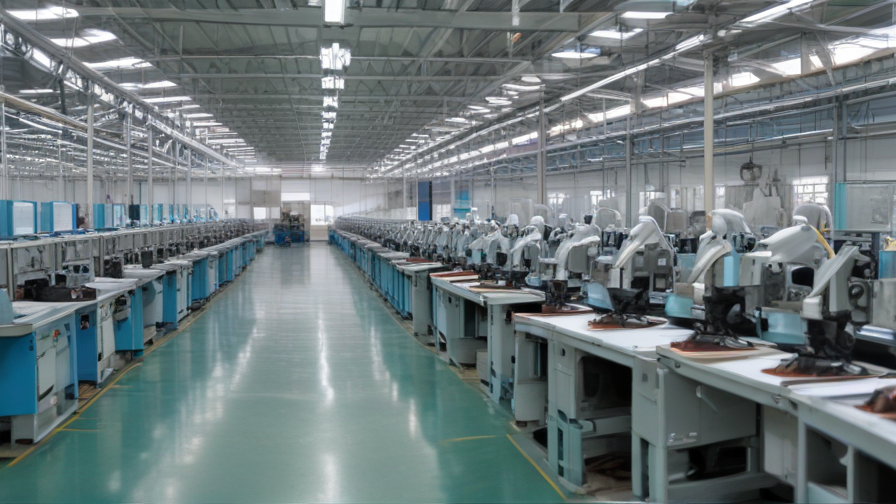
Price Cost Research for plastic part manufacturing manufacturers Companies in China, use temu.com and 1688.com
When researching prices and costs for plastic part manufacturing companies in China, two popular websites to use are temu.com and 1688.com. These platforms provide a wide range of plastic part manufacturers, allowing you to compare prices and offerings.
To begin your research, first identify the specific type of plastic part you need and the quantity you require. This information will help you narrow down your search on both websites. Next, enter relevant keywords into the search bar, such as “plastic injection molding” or “plastic extrusion.”
On temu.com, you can browse through a variety of manufacturers and contact them directly to inquire about their pricing and services. Make sure to provide detailed specifications for your plastic part to receive accurate quotes. Additionally, you can utilize the platform’s messaging system to communicate with multiple suppliers and compare their quotes.
Similarly, 1688.com offers a vast selection of plastic part manufacturers in China. You can filter your search results based on factors such as minimum order quantity, production lead time, and quality certifications. Take advantage of the platform’s chat feature to discuss pricing details and negotiate with suppliers.
By utilizing temu.com and 1688.com, you can efficiently conduct price and cost research for plastic part manufacturing companies in China. Remember to consider factors such as quality, production capacity, and delivery options when evaluating potential suppliers. Ultimately, your goal is to find a reliable manufacturer that offers competitive pricing and meets your specific requirements.
Shipping Cost for plastic part manufacturing import from China
When importing plastic parts from China, the shipping costs can vary depending on various factors such as the size and weight of the parts, the shipping method chosen, and the distance between the supplier and the destination.
For small plastic parts, air freight is a popular choice as it is fast and efficient. The cost of air freight is usually calculated based on the weight, size, and volume of the shipment. It is worth noting that air freight costs are generally higher compared to sea freight.
Sea freight is more cost-effective for larger shipments of plastic parts. The cost of sea freight is usually calculated based on the volume or weight of the shipment. Additionally, sea freight typically takes longer than air freight, so it is important to factor in the lead time when planning the import.
It is recommended to work closely with a freight forwarder who can provide competitive shipping rates and assist with customs clearance and logistics. By consolidating shipments or opting for cheaper shipping methods, such as sea freight, it is possible to reduce shipping costs.
Overall, shipping costs for importing plastic parts from China can vary but by selecting the right shipping method and working with a reliable freight forwarder, it is possible to keep the costs within a reasonable budget.
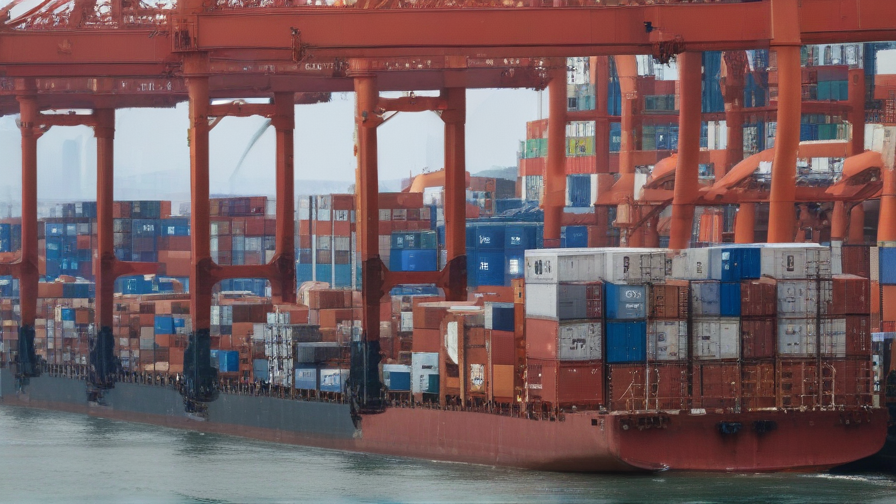
Compare China and Other plastic part manufacturing Markets: Products Quality and Price,Visible and Hidden Costs
China is known for its expertise in plastic part manufacturing, offering a wide range of products at competitive prices. The country has a strong infrastructure and skilled labor force, allowing for high-quality products to be produced efficiently. However, there have been concerns about the quality of products coming from China, with reports of counterfeiting and subpar materials used in production.
On the other hand, other plastic part manufacturing markets such as Europe and the United States are known for their strict quality control measures and use of higher quality materials. While the products from these markets may come at a higher price, customers can be assured of the durability and reliability of the products.
In terms of visible and hidden costs, China may offer lower upfront prices for plastic parts, but there may be hidden costs such as shipping fees, import duties, and quality control inspections. On the other hand, other markets may have more transparent pricing, but the higher upfront costs may deter some customers.
Overall, customers need to weigh the trade-offs between price and quality when selecting a plastic part manufacturer. While China may offer competitive prices, customers should be aware of the potential risks of lower quality products and hidden costs. Other markets may offer higher quality products at higher prices, but customers can be assured of the durability and reliability of the products. Ultimately, customers should prioritize their specific needs and budget constraints when choosing a plastic part manufacturer.
Custom Private Labeling and Branding Opportunities with Chinese plastic part manufacturing Manufacturers
Many Chinese plastic part manufacturers offer custom private labeling and branding opportunities for businesses looking to create their own branded products. These manufacturers can work with you to develop custom molds and designs for your plastic parts, allowing you to create unique and distinctive products for your customers.
By partnering with a Chinese plastic part manufacturer for private labeling and branding, you can take advantage of their expertise and experience in producing high-quality plastic parts at competitive prices. These manufacturers can help you create custom packaging, labels, and branding materials to ensure that your products stand out in the marketplace.
Working with a Chinese manufacturer for private labeling and branding also allows you to take advantage of their extensive network of suppliers and resources, making it easier for you to source materials and components for your products. Additionally, many Chinese manufacturers offer flexible production capabilities, allowing you to order small or large quantities of plastic parts to meet your specific needs.
Overall, partnering with a Chinese plastic part manufacturer for private labeling and branding can help you create unique, high-quality products that reflect your brand and vision. With their expertise and resources, you can develop custom plastic parts that will set your products apart from the competition and attract customers to your brand.
Tips for Procurement and Considerations when Purchasing plastic part manufacturing
When purchasing plastic part manufacturing services, there are several factors to consider to ensure you are getting the best value for your money. Here are some tips for procurement and considerations to keep in mind:
1. Quality: Quality is crucial when it comes to plastic parts, as they need to meet certain standards and specifications. Make sure to check the reputation of the manufacturer and ask for samples or references to verify the quality of their work.
2. Cost: While cost is an important factor, it should not be the only consideration. Look for a manufacturer that offers competitive pricing without compromising on quality. Consider factors such as volume discounts, tooling costs, and shipping expenses.
3. Manufacturing capabilities: It’s important to choose a manufacturer that has the capabilities to produce the plastic parts you need. Consider factors such as the type of plastic materials used, the size and complexity of the parts, and the production capacity of the manufacturer.
4. Lead times: Make sure to discuss lead times with the manufacturer to ensure they can meet your project deadlines. Delays in production can have a significant impact on your business, so it’s important to choose a manufacturer that can deliver on time.
5. Communication: Effective communication is essential when working with a manufacturer. Make sure to establish clear lines of communication and provide detailed specifications for your project. Regular updates and progress reports will help you stay informed throughout the manufacturing process.
By considering these tips and factors when purchasing plastic part manufacturing services, you can ensure you are getting high-quality parts at a competitive price while meeting your project deadlines.
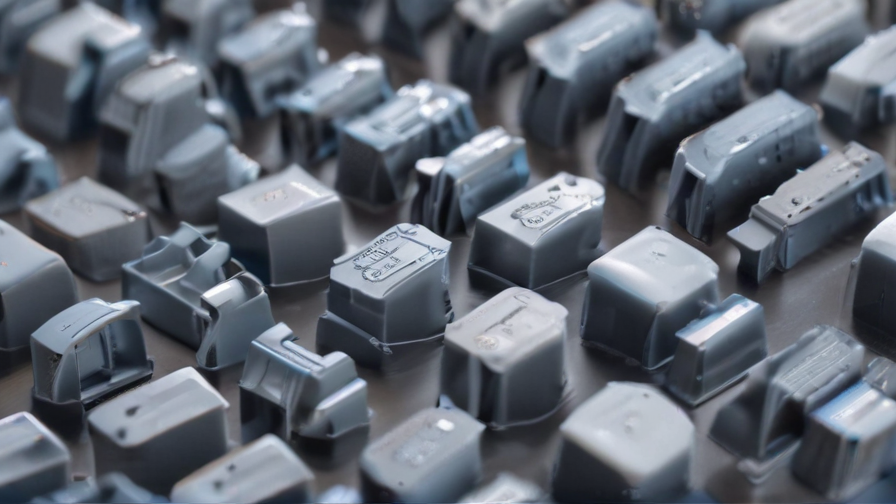
FAQs on Sourcing and Manufacturing plastic part manufacturing in China
1. Why should I consider sourcing plastic parts from China?
Sourcing plastic parts from China can offer cost savings due to lower labor and production costs compared to many other countries. China also has a well-established manufacturing infrastructure, a wide range of suppliers, and a strong expertise in plastic part manufacturing.
2. How do I find a reliable manufacturer for plastic part manufacturing in China?
You can start by doing thorough research, checking online directories and trade platforms, attending trade shows, and getting recommendations from other businesses. It is also essential to conduct background checks, request samples, and visit the factory in person if possible to ensure the manufacturer meets your quality and ethical standards.
3. What are the common challenges when sourcing plastic parts from China?
Some common challenges include language barriers, cultural differences, quality control issues, intellectual property concerns, and logistical complications. Working with a reputable sourcing agent or conducting regular quality inspections can help mitigate these risks.
4. What are the standard lead times for manufacturing plastic parts in China?
Lead times for manufacturing plastic parts in China can vary depending on the complexity of the part, production volume, and the manufacturer’s capacity. On average, lead times can range from 2-6 weeks for prototype and small batch orders, and 6-12 weeks for larger production runs.
5. How can I ensure quality control when manufacturing plastic parts in China?
To ensure quality control, it is crucial to establish clear specifications, conduct regular inspections, and communicate closely with the manufacturer throughout the production process. You can also consider working with third-party quality inspection agencies to verify the quality of the finished products before shipment.
Why contact sourcifychina.com get free quota from reliable plastic part manufacturing suppliers?
Sourcifychina.com provides a platform for connecting businesses with reliable plastic part manufacturing suppliers in China. By contacting Sourcifychina.com, you can access a network of trusted suppliers who have been vetted for quality and reliability.
Obtaining a free quota from these suppliers allows you to get an idea of the cost and feasibility of your plastic part manufacturing project without committing to a large financial investment. This can be particularly beneficial for businesses looking to test the waters in a new market or evaluate different suppliers before making a decision.
By leveraging the expertise and resources of Sourcifychina.com, you can streamline the sourcing process and ensure that you are working with reputable suppliers who can deliver high-quality plastic parts at competitive prices. This can ultimately save you time and money while also providing peace of mind knowing that your manufacturing needs are in good hands.
Overall, contacting Sourcifychina.com to get a free quota from reliable plastic part manufacturing suppliers is a smart business decision that can help you make informed choices and achieve success in your manufacturing endeavors.